FDM 3D Printing Services
High-Performance Prototyping & Production Parts in Advanced Thermoplastics
Industrial FDM 3D Printing Services
At Malcolm Nicholls Ltd, we specialise in industrial FDM 3D Printing services — a reliable, repeatable additive manufacturing process that delivers high-strength, functional parts using the same thermoplastics trusted in traditional manufacturing. With over 50 years of prototyping experience, our FDM services are trusted across motorsport, automotive, defence, aerospace, and medical sectors for mission-critical applications. We have the ability to print any Performance Thermoplastic on the market, from PLA to PEEK, PEKK, ULTEM™ , PPSU, and more.
Why Choose Industrial FDM?
Engineering-Grade Materials
Print in high-performance thermoplastics like ULTEM™, PEKK, PEEK, Nylon 12CF, and PPSU for demanding applications in regulated industries.
Durable, Functional Prototypes
FDM excels in rapid design validation for form, fit, and function, including working prototypes that undergo mechanical, thermal, and chemical testing.
Low-Volume & Bridge Production
Ideal for short runs, custom tooling, jigs and fixtures, and small-batch end-use parts without the lead times or tooling costs of injection moulding.
Tight Tolerance Capabilities
Our experience allows us to optimise print orientation and infill to achieve structural integrity and dimensional precision, even for anisotropic parts.
Design for Additive Manufacturing (DfAM)
We work collaboratively with your design team to reduce weight, consolidate assemblies, and achieve features that are impossible via subtractive methods.
Outstanding Material Performance
Capable of printing with high-performance thermoplastics that offer exceptional temperature resistance, superior chemical durability, flame and smoke compliance, high mechanical strength, and minimal off-gassing—ideal for demanding industrial and aerospace applications.
FDM Materials for Engineering & Production
We offer one of the UK’s broadest selections of industrial FDM materials, from general-purpose thermoplastics to advanced polymers for aerospace and medical use.
High-Performance Polymers
ULTEM™ 9085
- High strength-to-weight ratio, ideal for aerospace, automotive, and rail applications.
- Flame, smoke, and toxicity – FST rated
- Excellent thermal and chemical resistance, suitable for demanding environments.
- Lightweight and durable, perfect for functional prototypes and end-use parts.
- Certified-grade options available for traceability in regulated industries.
ULTEM™ 1010
- Highest heat resistance of any FDM material, with a heat deflection temperature (HDT) of 216°C.
- Excellent chemical resistance and mechanical strength.
- Autoclave-compatible, making it ideal for medical, aerospace, and food-grade applications.
- Available in certified grades, including ISO 10993 and NSF 51 for biocompatibility and food contact.
- Great for tooling, fixtures, and high-performance prototypes.
PEEK
- Steam-sterilisable
- Ideal for medical or composite tooling.
- Exceptional mechanical strength and stiffness, comparable to metals—ideal for demanding engineering applications.
- High temperature resistance, with a continuous use temperature up to 260°C, suitable for engine components and aerospace fixtures.
- Excellent chemical resistance, even in aggressive environments such as oil & gas or chemical processing.
- Naturally flame-retardant and low smoke emission, making it suitable for aerospace and transport
- Biocompatible and sterilisable, frequently used in medical implants and surgical instruments
PEKK
- Greater thermal stability and lower melt temperature than PEEK, allowing for easier processing while maintaining high performance
- Outstanding dimensional stability and low outgassing, ideal for aerospace, satellite, and space-bound components.
- Superior layer adhesion in 3D printing, resulting in better isotropic mechanical properties across all directions.
- Highly resistant to wear, fatigue, and chemicals, making it reliable for high-load or high-friction parts.
- FDA and aerospace-compliant grades are available and suitable for both structural and functional end-use parts
- Both PEEK & PEKK represent the pinnacle of polymer 3D printing, offering metal-like properties in lighter, corrosion-resistant forms—perfect for industries where performance cannot be compromised
PSU (Polysulfone)
- Ideal for medical or composite tooling.
- Exceptional mechanical strength and stiffness, comparable to metals—ideal for demanding engineering applications.
- High temperature resistance, with a continuous use temperature up to 260°C, suitable for engine components and aerospace fixtures.
- Excellent chemical resistance, even in aggressive environments such as oil & gas or chemical processing.
- Biocompatible and sterilisable, frequently used in medical implants and surgical instruments
- Naturally flame-retardant and low smoke emission, making it suitable for aerospace and transport
PPSU (Polyphenylsulfone)
- Higher impact strength and temperature resistance than PSU and PES, with use temps up to ~220°C.
- Outstanding chemical resistance, even to aggressive disinfectants and solvents, commonly used in medical sterilisation.
- High toughness and flame resistance, suitable for aerospace, automotive, and healthcare applications.
- Retains mechanical properties after repeated autoclave cycles, making it ideal for reusable medical devices.
- Naturally opaque, typically amber or black, and highly durable under mechanical stress
PPS (Polyphenylene Sulfide)
- Exceptional chemical resistance, second only to PTFE, ideal for chemically harsh environments.
- High temperature resistance, with a continuous use temp up to 220–240°C.
- Dimensional stability and low moisture absorption, making it perfect for precision parts in electronics and automotive.
- Inherently flame retardant and self-extinguishing, used in electrical housings, connectors, and structural parts.
- Excellent wear and fatigue resistance, suitable for high-performance mechanical applications.
Carbon-Fibre & Impact-Resistant
Nylon 12CF - Carbon-Fiber Filled Nylon 12
- Carbon fiber-reinforced for significantly increased stiffness, strength, and dimensional stability.
- Excellent strength-to-weight ratio, making it a lightweight alternative to metal for tooling and structural parts.
- Ideal for functional prototypes, jigs, fixtures, and end-use components requiring high rigidity.
- High thermal resistance, with a heat deflection temperature (HDT) of up to ~143°C.
- Strong chemical resistance and good wear properties, suitable for demanding industrial environments. Best-in-class performance among FDM materials for load-bearing applications.
- Requires a high-performance 3D printer with a heated build chamber for optimal results.
PC-ABS - Polycarbonate-Acrylonitrile Butadiene Styrene
- Combines the strength and heat resistance of PC with the flexibility and ease of printing of ABS.
- High impact resistance and toughness, ideal for functional prototypes and end-use parts.
- Good surface finish and detail resolution, great for cosmetic as well as structural components.
- Excellent strength-to-weight ratio, used across automotive, consumer products, and electronics.
- Thermal performance up to ~110°C, suitable for under-the-hood and industrial applications.
- Common for jigs, fixtures, housings, and enclosures that require durability and strength.
PC-ISO - Polycarbonate - ISO 10993
- Strong, durable, and heat-resistant, with biocompatibility certifications for medical and food-contact applications.
- Ideal for medical devices, surgical planning models, and food-grade tooling.
- Sterilizable via gamma radiation or ethylene oxide, suitable for cleanroom environments.
- Excellent clarity and strength, with good thermal resistance (HDT ~132°C).
- Used in healthcare, pharmaceutical, and food packaging industries where regulatory compliance is required.
- Both PC-ABS & PC-ISO leverage polycarbonate’s strength and thermal performance, but PC-ABS is geared toward general-purpose industrial use, while PC-ISO meets stringent medical and food safety standards.
General Purpose FDM Materials
ABS-M30
- Stronger and more durable than standard ABS, with improved tensile, impact, and flexural strength.
- Excellent for functional prototypes, end-use parts, and manufacturing tools that require toughness and reliability.
- Good surface finish and fine feature detail, ideal for concept models and assembly fit testing.
- Cost-effective material for a wide range of applications, including automotive, consumer products, and electronics.
- Supports soluble support structures, allowing for complex geometries and easy post-processing.
- Thermal performance up to ~96°C, suitable for moderate heat environments.
- ABS-M30 is a go-to material for engineers and designers seeking a balance of strength, accuracy, and affordability in their 3D printed parts.
ASA (Acrylic Styrene Acrylonitrile)
- Excellent UV resistance, making it ideal for outdoor applications and long-term exposure to sunlight.
- Strong mechanical properties, similar to ABS, with good impact strength and durability.
- Superior aesthetics, with a matte finish and excellent colour stability over time. Great weatherability, resistant to moisture, chemicals, and environmental stress.
- Supports soluble support material, enabling complex part geometries and easy post-processing.
- Ideal for functional prototypes, housings, enclosures, and signage.
- Thermal resistance up to ~96°C, suitable for exterior automotive parts and electrical casings.
- ASA is a top choice for applications where appearance and environmental durability are key, offering performance that rivals ABS with added weather resilience.
PLA - Polylactic Acid
- Excellent for durable concept models, housings, consumer product enclosures and fit-checks.
- Easy to print with excellent detail and minimal warping.
- Biodegradable and made from renewable resources.
- Ideal for prototypes, visual models, and displays.
- Low heat resistance (~60°C); not for load-bearing use.
- Smooth surface finish with minimal odour when printing.
TPU 92A - Thermoplastic Polyurethane
- Abrasion-resistant thermoplastic for gaskets, seals and functional elastomeric parts
- Flexible, durable, and impact-resistant material.
- Shore hardness of 92A—rubber-like feel with toughness.
- Great for seals, gaskets, grips, and wearable parts.
- Good chemical and abrasion resistance; bendable under stress.
- Requires careful print settings for optimal results.
FDM Capabilities at MNL
Infill Options
Ultralight (0–20%) – Fast, lightweight prototypes
Light (20–50%) – Balanced strength and cost
Solid (50–80%) – Maximum strength for functional parts
Layer Resolutions
Fine (100μm) – High visual fidelity, smooth finish
Standard (200μm) – Best balance of detail and speed
Economy (300μm) – Cost-effective for large volumes
Flexible Nozzle Options & High-Temperature Capability
Our nozzles range from 0.2mm to 1.2mm, we can offer the versatility to switch between ultra-fine detail and high-speed, large-format prints. Each nozzle is engineered to withstand extreme conditions, reaching temperatures up to 500°C—making our FDM manufacturing fully compatible with high-performance thermoplastics such as PEEK, PEI, and PPSU. This capability enables production of parts with exceptional strength, thermal resistance, and chemical stability, ideal for aerospace, automotive, medical, and industrial applications.
Challenge Metal Printing With Production-Ready FDM 3D Printing – Stronger Than Metal. Faster Than Traditional Manufacturing.
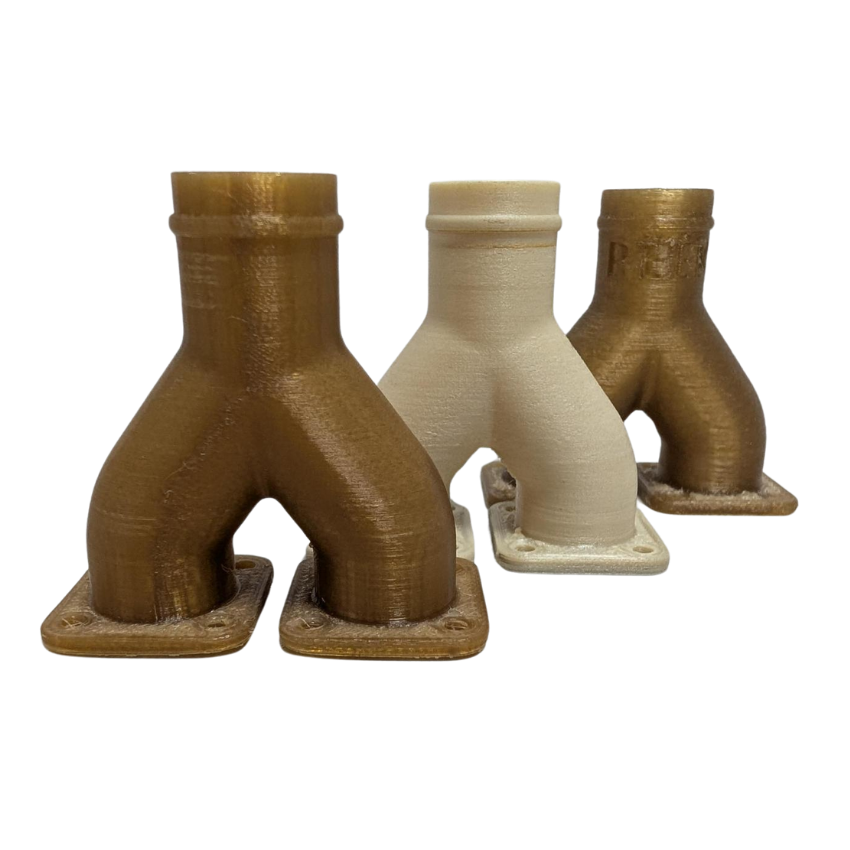
Bring your parts to life with our industrial-grade Fused Deposition Modelling (FDM) 3D printing services — ideal for high-performance parts in aerospace, automotive, motorsport, defence, and beyond.
Industrial Applications; We support clients across a wide spectrum of industries, including:
- Motorsport & Automotive – Lightweight brackets, housings, ducts, wind tunnel models
- Defence – Functional field components, test rigs, and drone parts
- Aerospace – Flame-retardant interior fittings, cable guides, tooling
- Medical – Sterile surgical guides, instrument housings, bio-compatible prototypes
- Consumer Electronics & Industrial Design – High-strength enclosures, design mockups, ergonomic tests
Pros and Cons of FDM 3D Printing
Explore the advantages and limitations of Fused Deposition Modelling to make informed decisions for your prototyping and production needs.
FDM Advantages
Cost-Effective Prototyping
No tooling required, making it ideal for quick-turnaround iterations and small batch runs
Wide Range of Engineering-Grade Materials
Supports high-performance thermoplastics (e.g., ULTEM™, PEEK, Nylon 12CF) for demanding industrial applications.
Strong, Functional Parts
Suitable for end-use components, not just visual models — especially when printed with solid infill and advanced polymers.
Fast Lead Times
Rapid print-to-part process reduces time to market and accelerates product development cycles.
Scalable Design Freedom
Easily print complex geometries, internal features, or part consolidation designs that are difficult or impossible to machine or mould
Minimal Waste
Additive process uses only the material needed for the part and support, reducing scrap compared to subtractive methods.
Limitations of FDM
Lower Resolution than SLA or SLS
Visible layer lines and slightly rough surface finish; may require post-processing for cosmetic parts.
Anisotropic Strength
Mechanical strength is lower in the Z-axis due to layer bonding, which can limit performance in certain orientations.
Limited Detail for Small Features
Not ideal for micro-detail or intricate surface textures — SLA or PolyJet may be more appropriate for fine cosmetic models.
Support Removal and Warping
Some geometries require breakaway or soluble supports, and large flat parts may warp if not printed with care.
Speed vs. Size Trade-Off
Large parts with high infill or fine layer resolution can take many hours or days to print.
FDM 3D Models and Projects
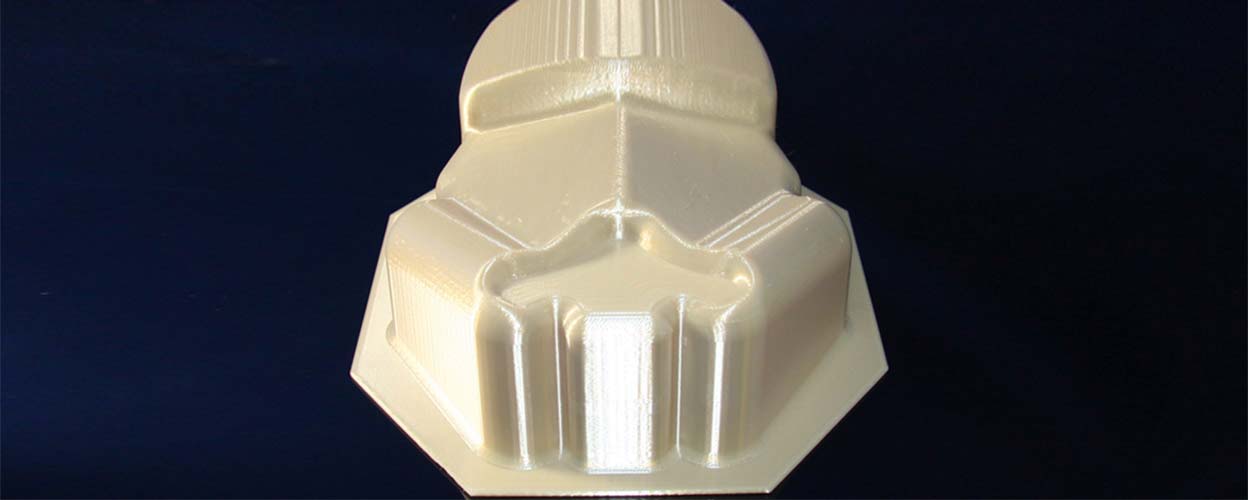
Storm Trooper Food Mould
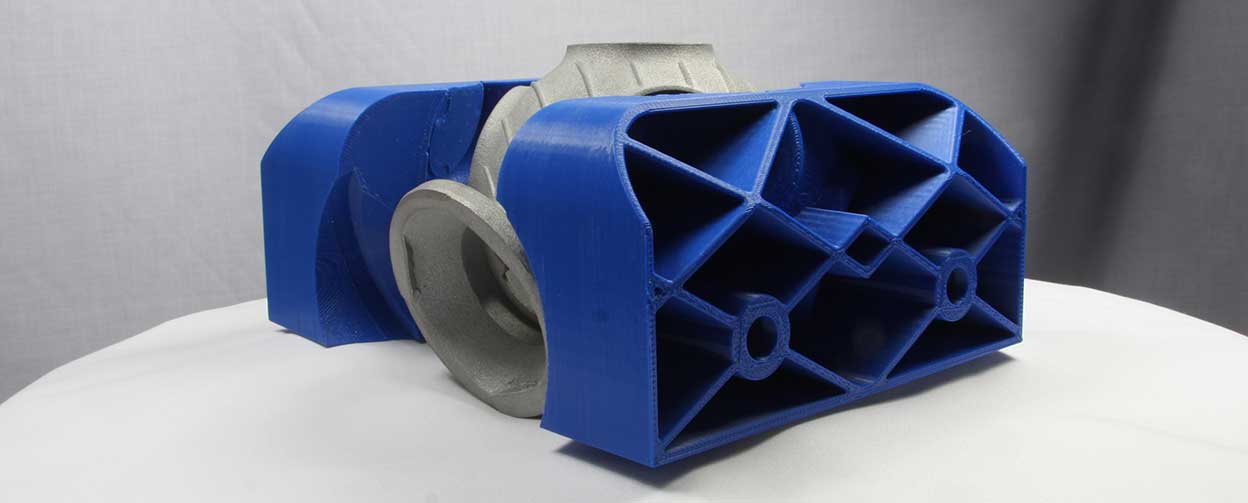
FDM 3D Printed Machining Jig
Get in touch
Address
Waterloo Industrial Estate, Waterloo Cres, Bidford-on-Avon, B50 4JH
Call Us
01789 490382
Email Us
quotes@mnl.co.uk