Fosters Beer Pump Prototype
Crafting High-Fidelity Prototypes
Beer Dispensing Font Prototypes
Case Study: Crafting High-Fidelity Prototypes
A client in the beverage industry required highly realistic prototypes for a new product launch. These prototypes needed to closely mimic the final production units, both in appearance and functionality, as they would be used extensively throughout the country in real-world environments.
To achieve the desired level of detail, a multi-faceted approach was employed. The lower half of the body needed to be fabricated in metal to enable a critical cooling and condensation effect. This metal component required meticulous polishing and a high-quality chrome plating for a flawless finish. Additionally, subtle engraving was added using a specialised rub-down technique.
The upper portion of the body was designed to incorporate lighting elements that would illuminate a brand logo and text. A black segment needed to act as a mask, precisely controlling light emission. The client’s original concepts were expertly transformed into master models using a combination of Stereolithography (SLA) and Selective Laser Sintering (SLS) 3D printing processes. A team of skilled model makers then provided the necessary finishing touches to these masters.
From the completed masters, silicone tooling was created. For the metal components, investment casting waxes were produced from the rubber tools. In a specialised foundry, these waxes were used to create brass castings. Finally, a dedicated finishing team transformed both the raw metal castings and the plain white polyurethane (PU) castings into stunning replicas, flawlessly representing the client’s vision.
This project successfully produced multiple sets of fully functional prototypes within a remarkably short timeframe, demonstrating the power of combining advanced 3D printing techniques with traditional craftsmanship.
Interested in learning more about how we can help?
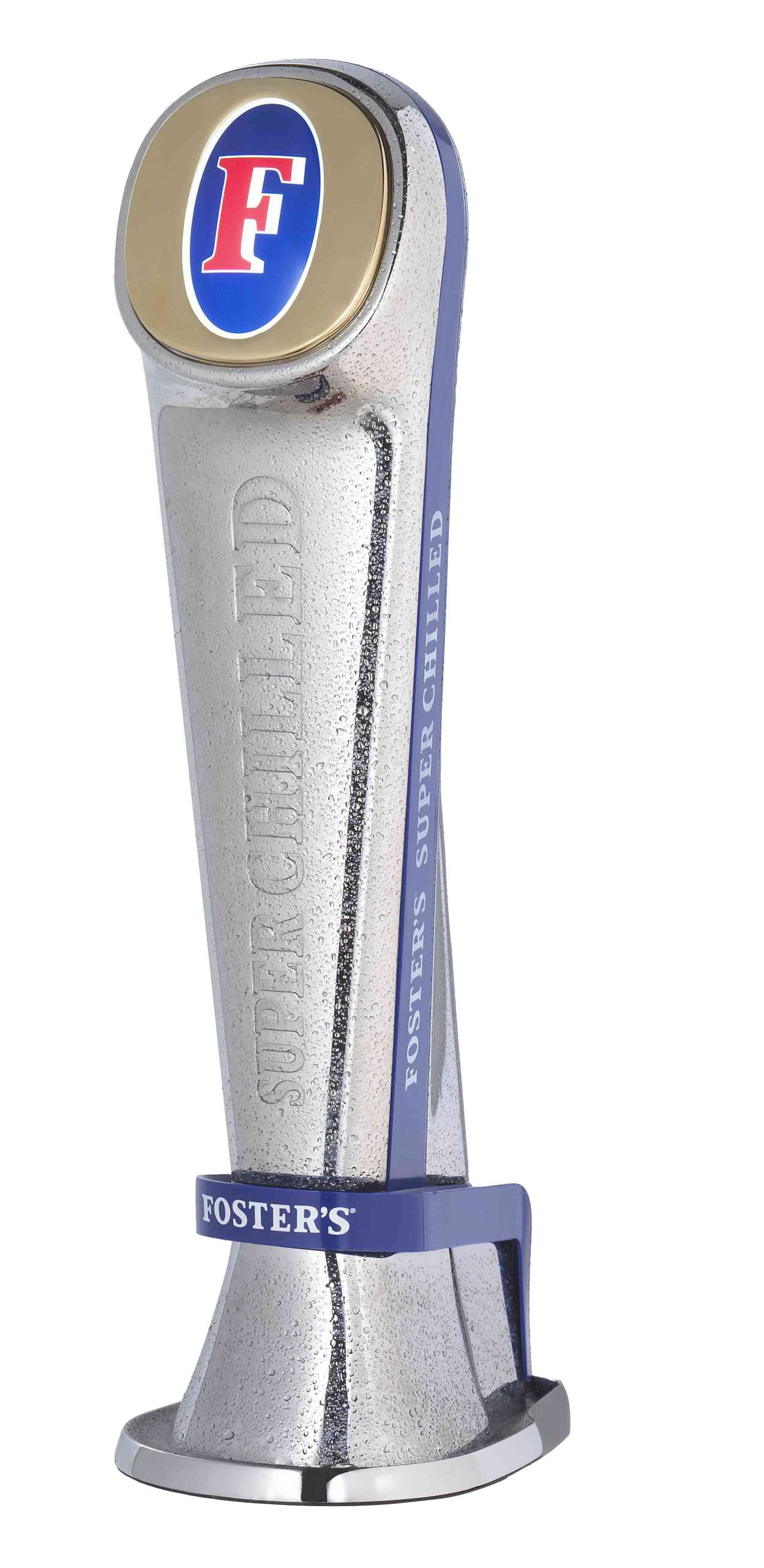