Range Rover Evoque
Malcolm Nicholls Ltd (MNL) was approached to work alongside our client to produce flawlessly finished colour swatches for a range of new Range Rover Evoques. Utilising our low volume manufacturing techniques
Evoque Colour Swatches
Malcolm Nicholls Ltd (MNL) were approached to work alongside our client to produce flawlessly finished colour swatches for a range of new Range Rover Evoques.
The Process
MNL produced the colour swatches using our 3D printing methods. Utilising one of our Stereolithography (SLA) machines to produce a master pattern, our highly skilled traditional model makers were able to hand finish each colour swatch.
The master pattern had to have a perfect high gloss finish so that this would be emulated on further castings. Once the model was finally finished a silicone tool was produced and subsequent castings followed – a process we advocate for clients looking to produce in lower volumes.
The casting then went to MNL’s finishing department to have its topcoat of water-based paint applied in the correct pantone colour, matching the final production car. The casting then had their final coat of durable lacquer applied, in total using our low volume production methods the client was able to produce around 30 colour swatch cars and still have the ability to produce more by utilising their silicone tool.
The whole process was turned around very quickly, our client was able to use the colour swatches in showrooms across the country to demonstrate the colours of the new Range Rover Evoque.
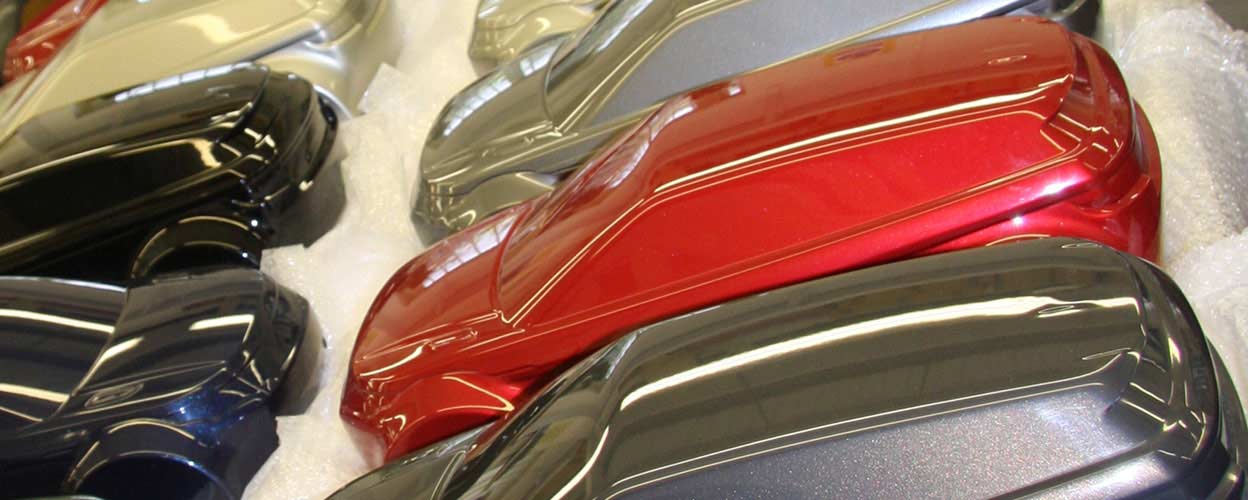
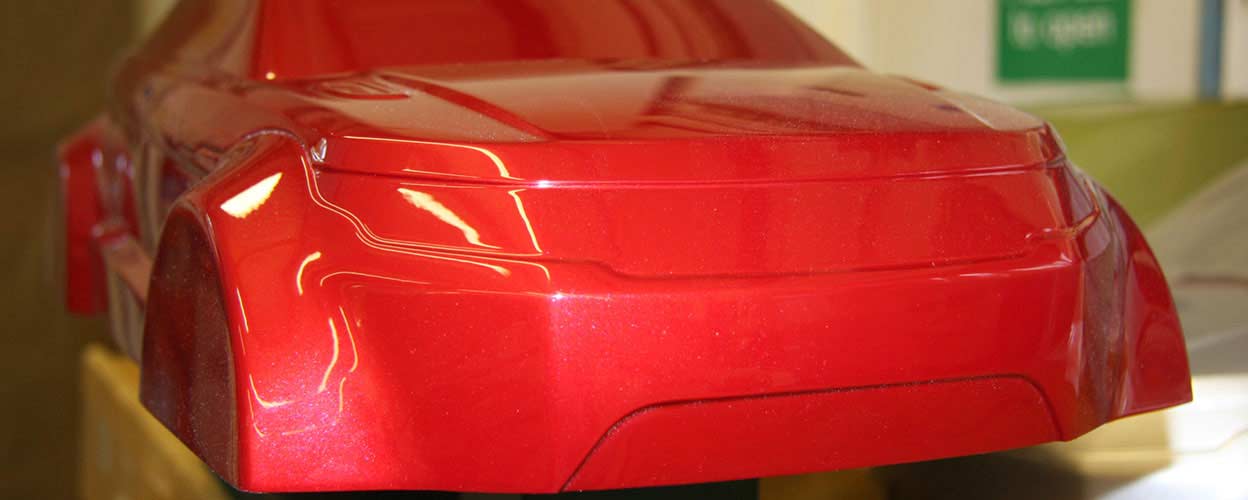
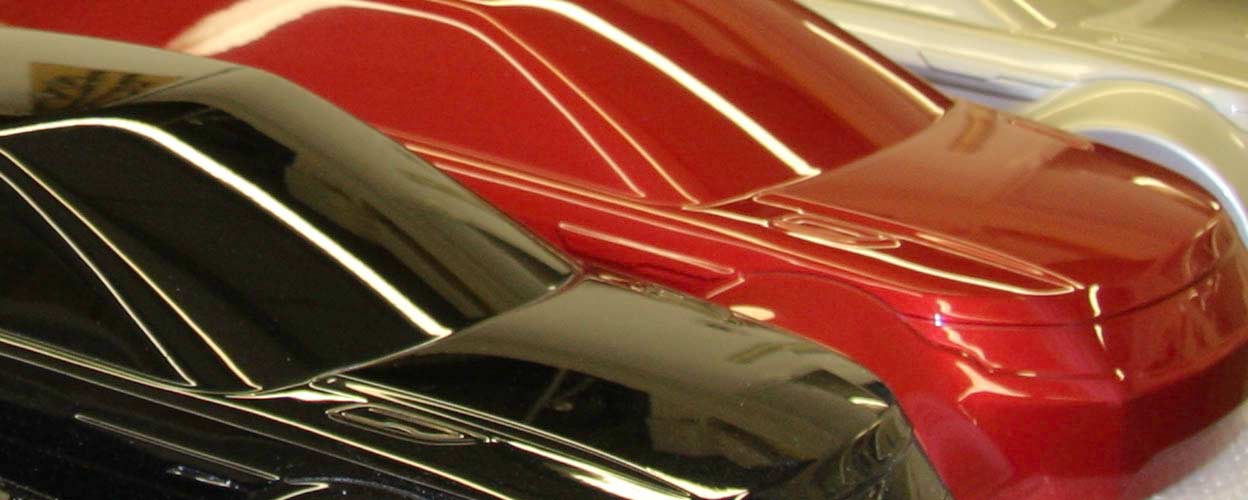
Why Use Low Volume Production / Low Volume Manufacturing?
With the growing demand for Low Volume Production also known as low volume manufacturing and small batch production Malcolm Nicholls Ltd can produce 1 – 1000’s of parts.
If you’re looking for a one-off bespoke top-quality part such as a trophy, or you require 1000’s customised parts such as widgets, we have the solutions to suit your needs.
It is an increasingly popular option as it allows for a smaller investment in tooling and materials while providing fast access to the market. It also acts to bridge the gap between initial prototypes and mass production.
Historically, manufacturing components in low quantities has always been a costly exercise. With the advent of 3D printing and vacuum casting many constraints previously faced can now be significantly reduced. Technologies such as SLS (Stereolithography) and FDM (Fused Deposition Modelling) can now be used (especially for non-seen parts), to produce components in quantities as low as 1s and 2s and up to thousands, but still with exceptional material properties such as flame retardancy and high-heat requirements. Traditional design constraints, usually associated with injection mould tooling for example, can now be ignored enabling designers to be more efficient and reduce part count within assemblies.
Looking to Produce Multiple Parts?
We can produce anything from one to thousands