Comprehensive Guide To Vacuum Casting
At Malcolm Nicholls Ltd, we pride ourselves on pushing the boundaries of manufacturing innovation. In our commitment to offering cutting-edge solutions, we delve into the realm of overmoulding and insert moulding in vacuum casting—a game-changer in custom prototyping and on-demand production parts.
Understanding Vacuum Casting Overmoulding: Elevating Your Design Vision
Overmoulding is a sophisticated process where a secondary layer of material is seamlessly applied to an existing substrate within a vac casting. The result? A fusion of materials that enhances functionality, durability, and aesthetic appeal. This technique is a boon for the new product development cycle, offering unparalleled design versatility. In prototyping, it allows for the creation of intricate, detailed parts with varying material properties, providing an accurate representation of the final product. Furthermore, overmoulding in vac casting shines in low-volume manufacturing, offering a cost-effective solution for producing small batches of high-quality components. Our facilities are equipped to elevate your projects with precision and efficiency.
Material Bonding: Precision in Every Layer
Chemical bonding between overmoulded materials is achievable, but material compatibility is key to achieving the desired bond strength. Incorporating an adequate mechanical bond is highly recommended for critical applications. If the materials do not bond completely, there is a need for undercuts and indents to better connect the substrate and over mould. At Malcolm Nicholls Ltd, we prioritise the meticulous details, ensuring that each layer not only complements the other but forms a robust and reliable whole.
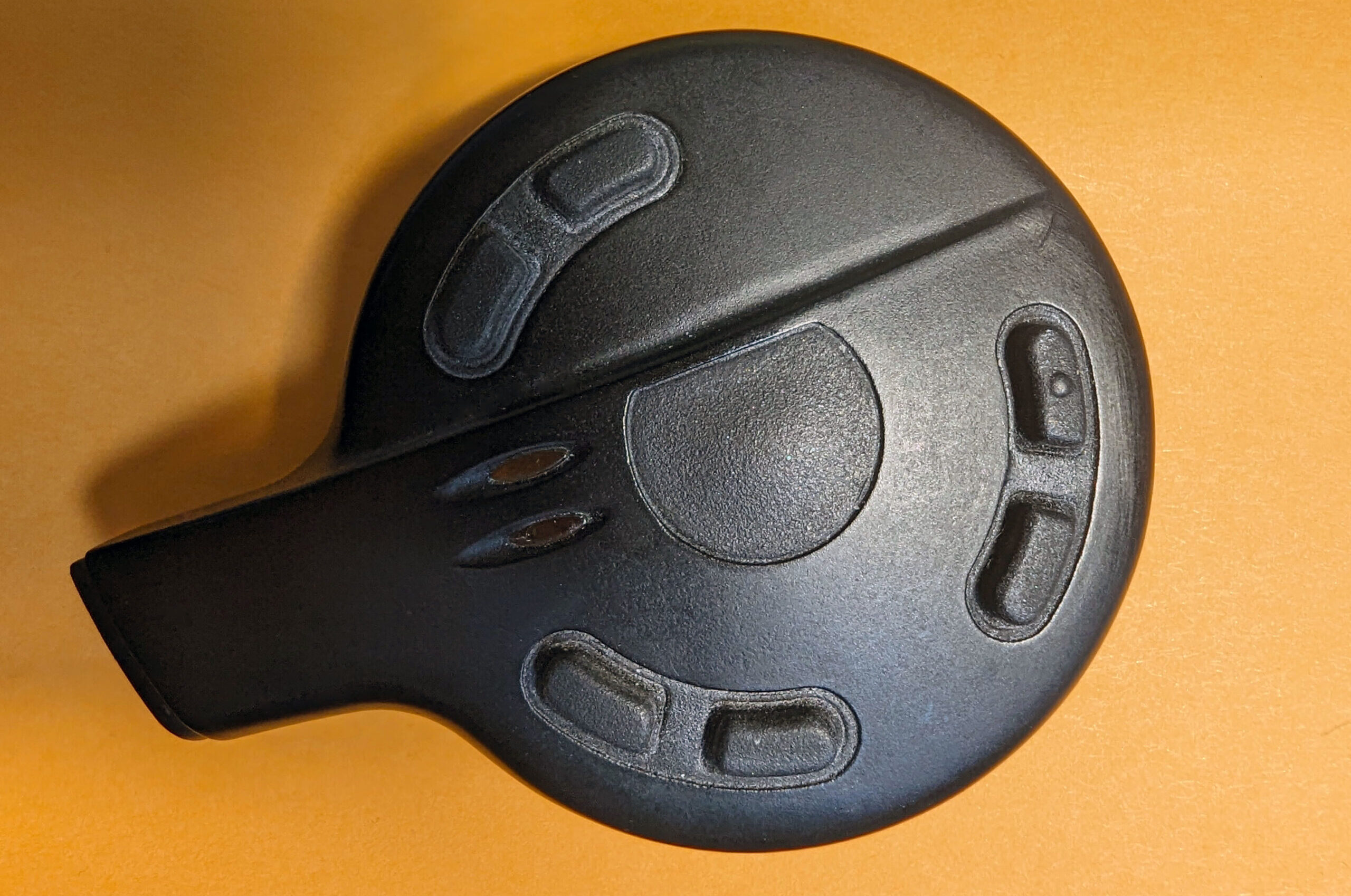
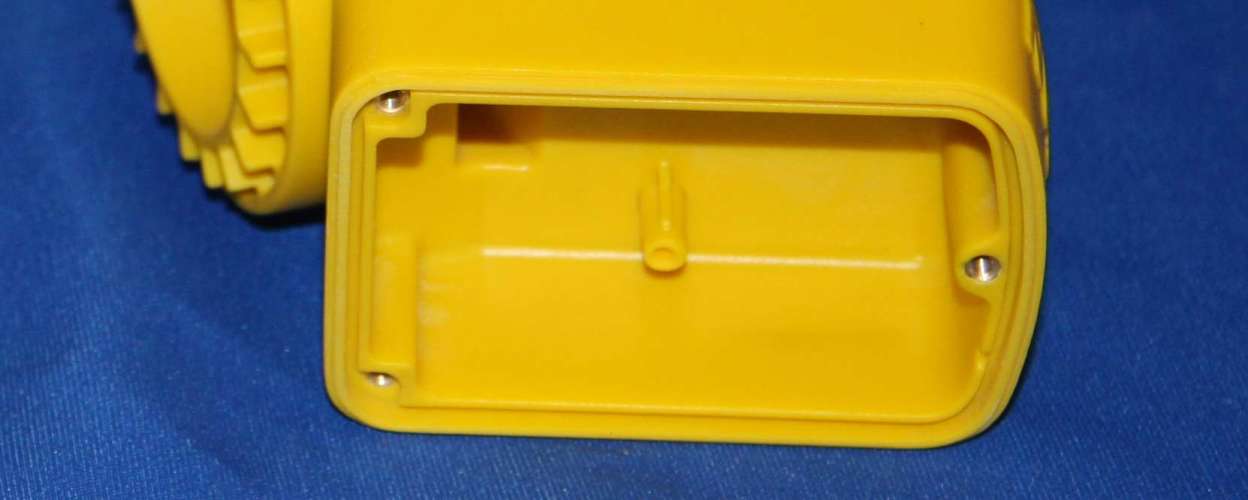
Insert Moulding: Threading the Path to Perfection
In the intricate landscape of custom prototypes and on-demand production, insert moulding plays a pivotal role. It involves the incorporation of pre-formed components, such as threaded inserts, seamlessly into the moulding process. This method is particularly advantageous for applications where threading is essential. Our facilities are equipped to handle the intricacies of insert moulding, ensuring that your components boast the precision and functionality your projects demand.
Why Use Threaded Inserts in Vacuum Casting?
Threaded inserts are favoured in vacuum casting for their capacity to enhance strength, durability, and precision in threaded connections. These inserts, made from materials compatible with the surrounding elements, contribute to uniform assembly and disassembly ease. Beyond their cost-effectiveness, threaded inserts provide versatility in design, accommodating complex orientations and locations within cast parts. Their use minimises material waste by enabling precise material placement, selective material usage, and efficient prototyping. Strategically placed before casting, these inserts optimise material resources and minimise excess. The ability to disassemble and reassemble components facilitates testing without the risk of damage, reducing the need for replacements and associated waste. Additionally, the reusability of moulds in vacuum casting extends their lifespan, decreasing the overall waste generated from mould production. This approach to threaded inserts not only enhances manufacturing efficiency but also contributes to a more sustainable and resource-conscious production process this also aligns with sustainability goals. Overall, threaded inserts offer an efficient and reliable solution for creating secure threaded connections in vacuum-cast parts, making them a valuable choice for applications ranging from prototypes to low-volume production.
Looking to Produce Multiple Parts?
We can produce anything from one to thousands
Vacuum Casting OverSeals and Gaskets
Vacuum Cast Overmoulding emerges as an optimal solution for manufacturing integral seals or gaskets, showcasing its versatility in yet another application. Tailored to meet the specific requirements of components, thin sections can be seamlessly cast in soft grades of polyurethane (PU), resulting in highly compliant seals adept at preventing leakage of liquids, dust, or powders. This application proves invaluable, especially in the creation of prototypes destined for rigorous functional testing.
Moreover, opting for vac casting overmoulded seals instead of traditional liquid sealants brings added advantages. Components designed with these seals allow for easy disassembly and reassembly during testing, fostering a more streamlined and efficient testing process. The ease of handling during testing makes overmoulded seals an ideal choice for prototypes, facilitating a thorough examination of functionality.
The polyurethane grades utilised in our overmoulding processes boast resistance to acids, bases, oils, and fuels. However, to ensure optimal material compatibility, we recommend customers engage in a collaborative discussion with our team. This proactive approach ensures that the selected materials align perfectly with the specific needs of the project, upholding our commitment to delivering reliable and tailored solutions.
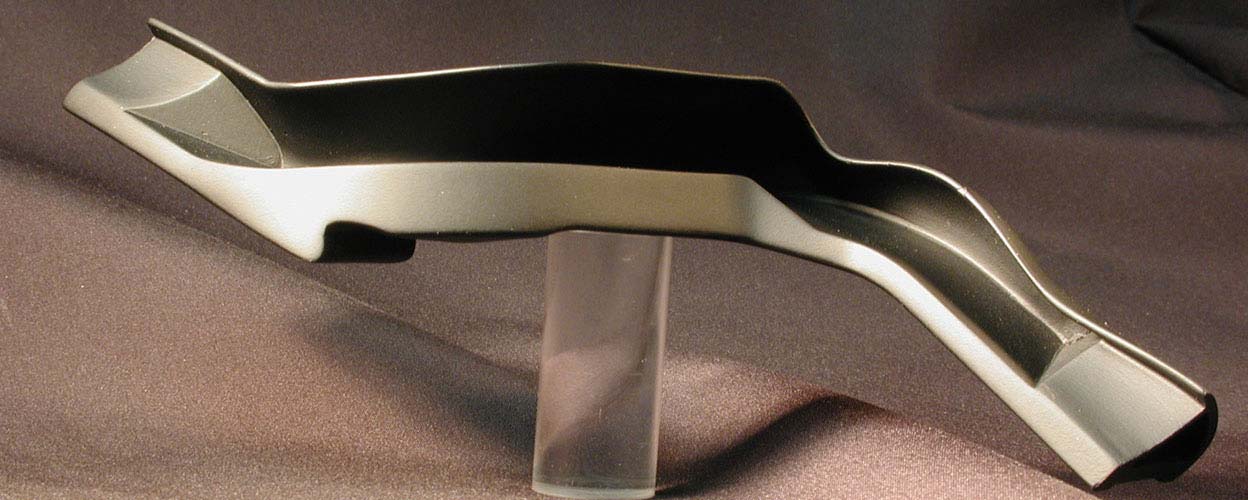
Compression Limiters
They play a crucial role in contributing to the structural longevity of the final product. These cylindrical devices, typically made of materials like brass or stainless steel, are strategically placed within the mould before the over-moulding process. Compression limiters play a crucial role in the realm of vacuum casting and overmoulding, preventing material overloading in a wide range of industries where plastics or plastic composites have become the go-to choice, gradually replacing traditional metal applications. The necessity of compression limiters becomes evident during the assembly process, particularly when tightening bolts where it generates compressive loads and forces that can potentially deform or even break the plastic materials. These limiters serve as a protective measure, ensuring that the structural integrity of your plastic components remains unscathed, even amidst the application of such compressive forces during assembly.
Overmoulding Simulated or Actual?
We have termed this as such to mean that the substrate and overmoulding are made separately and the over moulding is then glued to the substrate.
Simulated Overmoulding – Unveiling Possibilities in Design Verification and Intricate Parts
Simulated overmoulding serves as a valuable tool in the product development cycle, particularly during design verification and the creation of intricate parts. This technique allows manufacturers to replicate the effects of overmoulding without actually applying the additional layer of material. By utilising simulated overmoulding, designers can assess the feasibility of their concepts, verify the functionality of intricate details, and identify potential challenges in the manufacturing process. This approach is particularly useful when experimenting with various design iterations or when the final production requires meticulous attention to detail. Simulated overmoulding provides a cost-effective and efficient means of refining designs before committing to the actual overmoulding process, ensuring that the end result meets the highest standards of quality and precision, one thing to note is that not all geometries are possible with this process.
Actual Overmoulding: When Enclosure is Essential or Gluing is Impractical
Actual overmoulding takes centre stage in scenarios where it is essential to fully enclose a part or when traditional methods such as glueing prove impractical. This method ensures a seamless, integrated finish, enhancing the part’s durability and overall performance. In applications where components need to be enclosed for protection against environmental factors or when it is impossible or inefficient to use adhesives, actual overmoulding stands out as a reliable solution. The process not only strengthens the bond between materials but also contributes to the aesthetics and functionality of the final product. Whether it’s for weather resistance, improved grip, or simply achieving a cohesive design, actual overmoulding is the go-to choice for ensuring the integrity of components in diverse industries. Controlling ‘flash’ using silicone tooling for vacuum casting over moulding is a particular skill and MNL has perfected over years of experience.
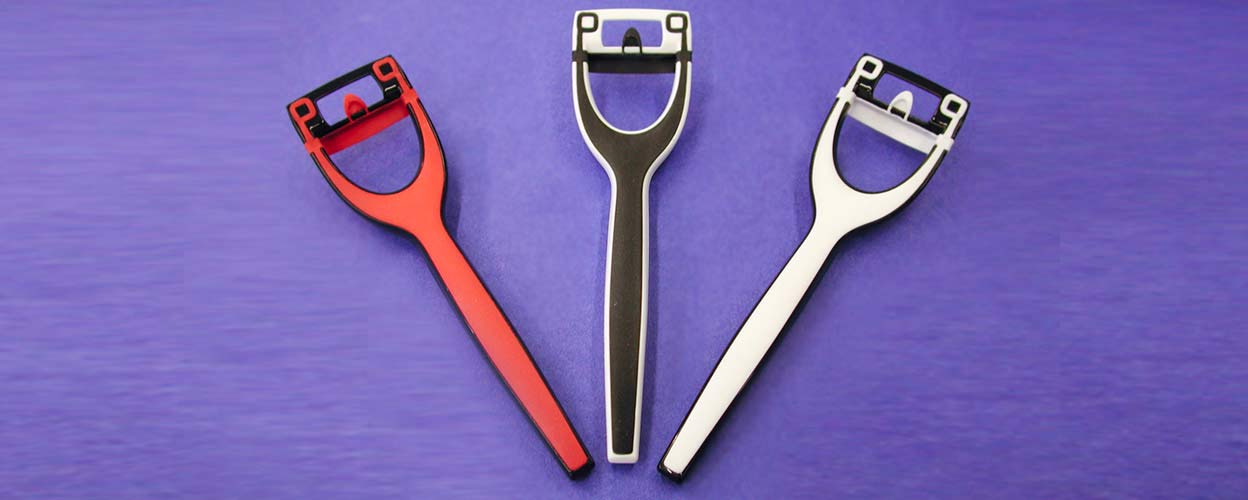
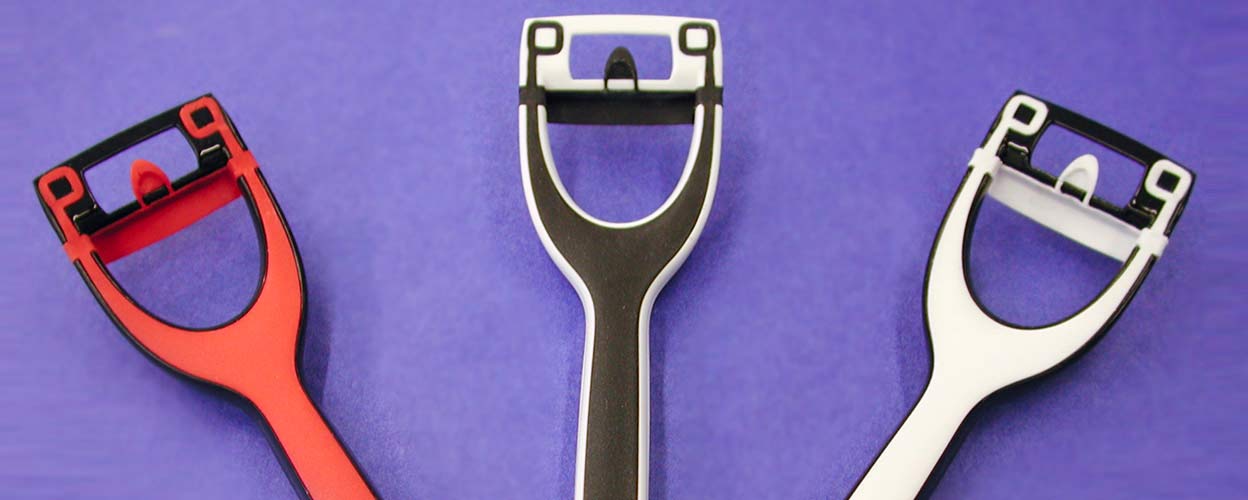
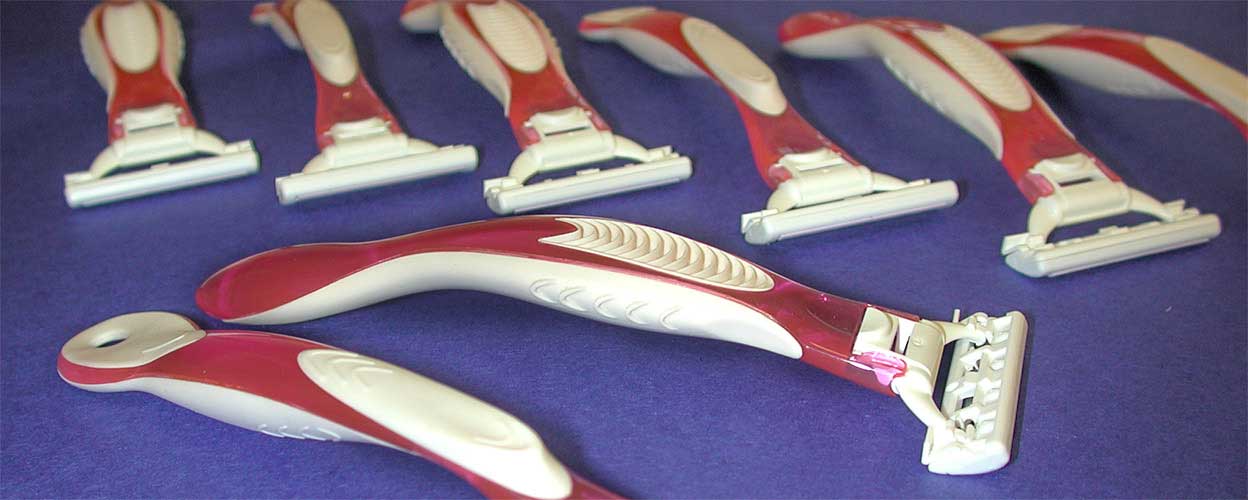