




Automotive 3D Printed Tyre Mould – Investment Cast
The CAD department at MNL started the 3D Printed Automotive Tyre Mould project by converting 2D developments of the tread pattern into 3D solid models of tyre segments. To prevent harmonic road noise problems, differing segment widths are positioned around the circumference of the tyre, with up to 10 or more different widths being utilised in the 70-80 segments necessary to make up one tyre. The mould segments were designed directly from the tyre segments.
Quickcast™
From the 3D data, 3D printed masters (*Quickcast™) were produced to enable the customer’s own foundry to produce aluminium castings of the tyre mould segments. Over various projects, the customer used MNL’s different options for producing the required 3D printed masters, dependent upon the quantities required. These options are; quickcast SL patterns for investment casting; thick-skinned shelled patterns for sand casting and solid SL patterns for ceramic gravity castings.
Take a look at the close-up view of the Automotive Tyre this shows evidence of the 3d printed build layers from the stereolithography process, We purposely left on the pattern to aid in the venting of air during the injection moulding of the rubber.
*QuickCast™ is a SLA® build style trademarked by 3D Systems and was created to meet the needs of the Investment Casting industry. 3D printing in general has dramatically reduced time to market, and utilising QuickCast patterns for investment casting has had the most profound effect on the 3d printing industry. QuickCast replaces the time-consuming process of creating tooling to produce wax patterns and allows for the review of metal designs in a matter of days instead of months.
The QuickCast build style consists of a hollow SLA pattern with an internal hexagonal support structure that adds strength to the pattern, this allows for easy drainage and facilitates the collapse of the pattern during thermal expansion to help avoid cracking the shell.
QuickCast patterns can provide several advantages compared to other direct patterns including low moisture absorption, high finish, dimensional stability and the capability of producing large assemblies.
Found the Automotive 3D Printed Tyre Mould Case Study Interesting?
Learn more about how we can help
Got a project we could help with this minute? Upload your files for quotation here...
Get Quote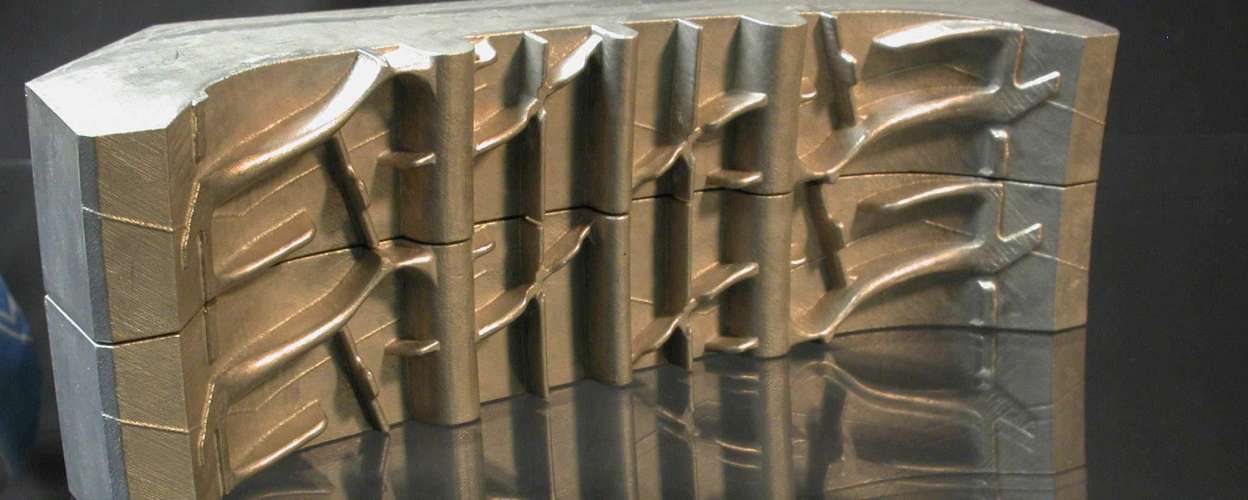
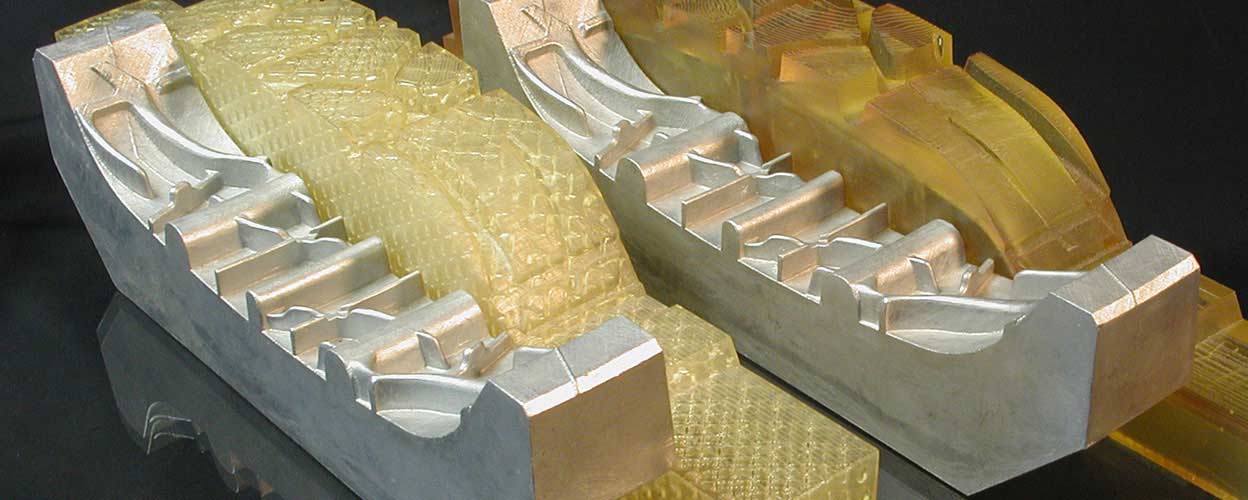