SLS Printing Services
Selective Laser Sintering (SLS) is a 3D Printing technology that is ideal for producing industrial strength parts on demand.
What is SLS printing?
Malcolm Nicholls Ltd and SLS 3D Printing
“SLS Rapid Prototyping for functional high-strength components – without the need for tooling”
How does SLS printing work?
With new layers being deposited on top of the first one and the process repeating itself until the very last 2D section of the part is produced. The last step is taking the part out that is now buried within the unsintered powder, we then de-cake the part (removing all of the powder) and take it to our workshop for any additional client finishing requirements.
SLS 3D Printing Applications
- Nylon / Glass Filled Nylon
- Test your first rapid prototype without the fear of breakage
- Acts like moulded components, strong and durable
- Excellent for fit and function. Ideal for clip features, hinges and snap-fit connections
- Build more complex structures than SLA as no supports are required
- High chemical resistance. High-Temperature resistance
- Durable patterns for sand casting
- The superior surface, straight from the machine
- For a detailed material datasheet download here
- Foundry Patterns
The benefits of SLS Rapid Prototyping
- Built from successive layers, SLS rapid prototype parts are laser fused to produce a 3D product with an exceptional range of properties
- High strength and rigidity
- Excellent mechanical properties
- Functional, high-quality plastic parts
- Stable over long periods of time
- Moveable parts abrasion resistance
- High resolution and selectivity
- High chemical resistance
- Food contact compliant
- Medical application appropriate
- Please get in touch for details of compliance with regulatory requirements.
- Support systems not required
Selective Laser Sintering (SLS) Materials
What is PA2200 SLS?
PA2200 is a fine, white powder with a well-balanced property profile which makes it an ideal choice for a wide variety of applications. Laser-sintered parts using PA 2200 possess excellent material properties including:
- Long-term stability along with high strength and stiffness
- Fully functional, high-quality plastic parts
- Excellent mechanical properties make it an ideal substitute for common injection moulding plastics
- Ideal for parts with movable components due to its high abrasion resistance
- Biocompatible according to EN ISO 10993-1 and USP/level VI/121 °c, allowing its use in medical applications e.g. for prostheses
- Approved for food contact in compliance with the EU plastics directive 2002/72/EC (exception: foodstuffs with high alcohol content)
- Good chemical resistance
- Ecological valuation – US Pharmacopeia Class VI Approved
Why choose MNL’s SLS printing service?
If you’re looking for high quality SLS printing services, MNL is the perfect choice. We use the latest technology and equipment to produce stunning results that meet your specific needs and requirements.
To find out more about our Selective Laser Sintering printing service, contact us today and we’ll be happy to answer any questions you have and provide you with a free quote.
Using SLS to Produce a Unique Piece of Art
SLS Models and Projects
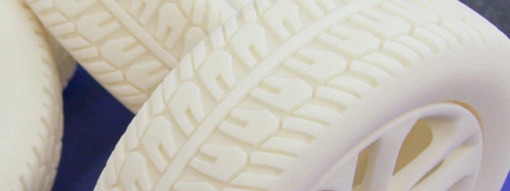
3D Printed Using the SLS Process
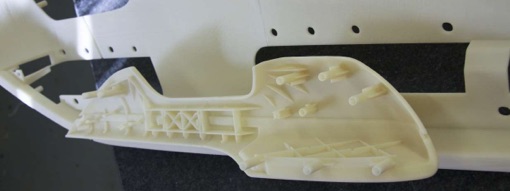
Functional or Working Prototypes
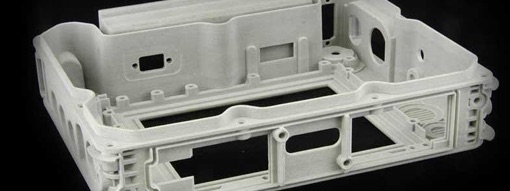
Glass and Aluminium Filled Nylon
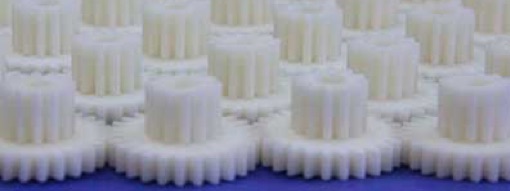
Additive Manufacturing
Choose a method to get your prices
Online instant quote
Upload data
Request a call back
Speak to us
Get in touch
Address
Waterloo Industrial Estate, Waterloo Cres, Bidford-on-Avon, B50 4JH
Call Us
01789 490382
Email Us
quotes@mnl.co.uk