Low Volume Manufacturing The Benefits
3D Printing
Low Volume Production
3D Print Finishing
Firstly, a short mention about Volume Manufacturing
Before we go in-depth about low-volume manufacturing – or low volume production – let’s make a few statements about volume manufacturing.
Traditionally, to make a light switch as an example, you would need complex, fully automated injection moulds costing thousands of pounds and taking weeks if not months to produce before production can begin. In some cases (like a car bumper) these costs can be in the 100’s of thousands and up to a year to produce.
These very high costs are often “amortized” over the large quantities of parts to be made from these mould tools. Therefore, the piece-part costs are not too adversely effected.
However, when quantities required for production runs are low, then these high tooling costs often render the project unviable.
It is at this point that other strategies and methods are required for production.
Low volume manufacturing is a manufacturing process, method or service for low quantities. The manufactured items can be produced by a choice of a multitude of methods depending upon many factors.
Low volume manufacturing services – There are many choices of available services or methods for low volume manufacture and we shall discuss many of the available options and the reasons why each method may be chosen over others.
Factors affecting the method to be used for low-volume manufacturing
There are many factors that may influence the chosen method for low-volume manufacture.
The main driving factors include:
- Desired quantity
- Size and complexity of the part
- Required surface finish
- Colour
- Material requirement (strength, temperature, fire retardancy etc)
Low Volume Injection Moulding
Injection moulding is the manufacturing process for producing parts by injecting molten material into a mould. Moulds are made from hardened tool steel and designed with fully automated moulding assistance such as ejection and robot handling for removal of moulded parts. Injection moulding can be performed with various materials, including metals, glasses, elastomers, confections, and most commonly, thermoplastic and thermosetting polymers. Malcolm Nicholls ltd specialise in polymers and elastomers.
Low volume injection moulding is where the moulds are made from less durable metals (often aluminium) cheaper and quicker to machine. They are less automated to run. The outcome is a cheaper and quicker mould tool to produce at the slight expense of piece-part cost.
Part quantities can still be in their thousands, but most importantly parts can be made from standard plastics.
Benefits of Low Volume Injection Moulding include:
- Excellent surface finish
- Material choice is the same as for volume manufacture
Disadvantages of using Low Volume Injection Moulding
- Relatively high cost for tooling, but still cheaper than high volume.
- Still a long time-frame for tooling to be ready for production.
Vacuum Casting
Low volume vacuum casting is the process for replicating parts from rubber moulds using PU resin materials. This method has been traditionally used in product development, however modern PU materials are much more suited to production requirements then they were in the past.
Benefits of vacuum casting include:
- Very quick method to get parts into production. A silicon rubber tool can be produced with a few days of a master model being produced.
- Extremely cost-effective. Tooling is often less than 10% of the cost of injection mould tools.
- The design constraints of injection moulding can be abandoned. As an example, undercuts hardly cause issues with this method.
Disadvantages of using vacuum Casting
- Silicon rubber tools have very short lifetimes, often making only 20-30 parts before requiring to be remade.
- Choice of materials is somewhat limited.
- Process is usually done by hand, this may lead to slight variation within the production batch.
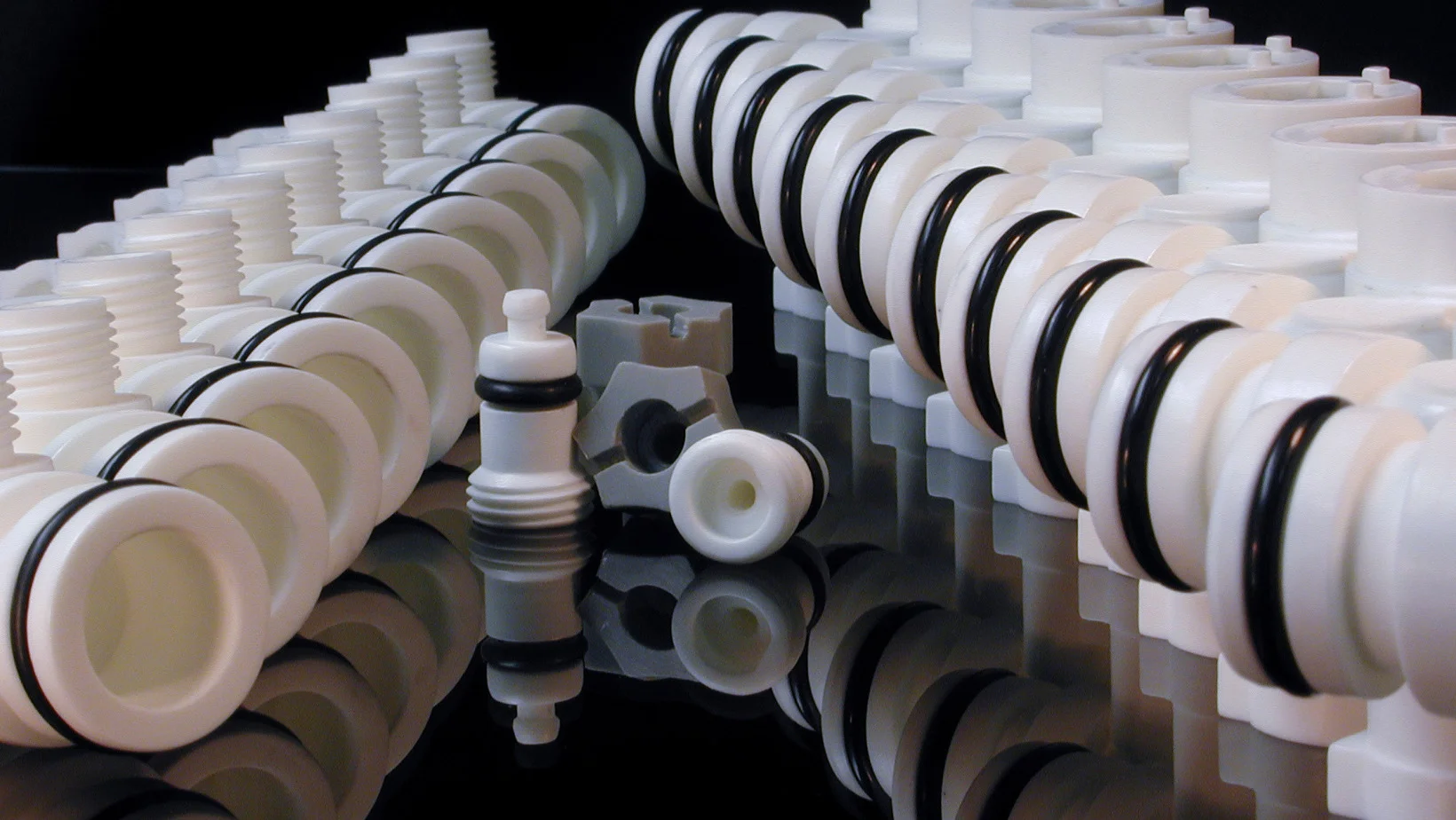
3D Printing
A process of creating three-dimensional objects from a digital file. A 3D printed object is created using additive processes, where successive layers of material are laid down (added) in different shapes.
There are many different types of 3D printing each with its own pros and cons.
Benefits of 3D Printing include:
- Speed of turnaround, small batches can be produced in an adhoc basis within days.
- No tooling requirements
- More complex part geometries possible.
Disadvantages of using 3D Printing
- Surface finish. 3D Printing layers provide undesirable surface finish.
- Material choice is not as diverse as injection moulding.
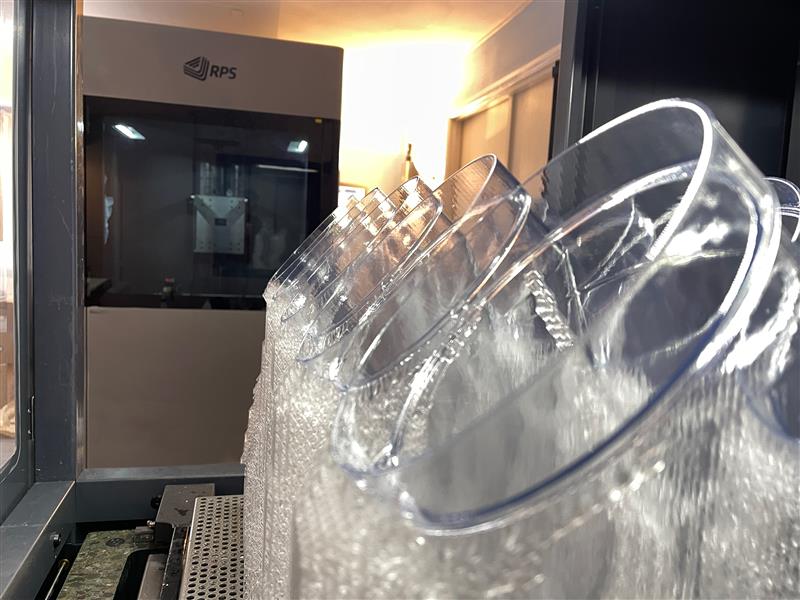
RIM Moulding
Almost a hybrid of injection moulding and Vacuum Casting. PU resin is injected into rigid tooling/moulds. The moulds are often made from special tooling resin via machining or pouring the liquid version over master models. The PU resins are injected into the moulds and allowed to set over time (typically from 5 mins to 30 per part).
Benefits of RIM Moulding include:
- Tooling is significantly cheaper than injection moulds.
Tooling Is also much quicker to produce than injection moulds.
There are plenty of material choices for RIM, many of which have been used in production for years.
Disadvantages of using RIM Moulding
Tooling is still significantly high cost for very low quantities (less than 100).
Most RIM materials are black and ONLY black.
Surface finishes are usually inferior to injection moulding, often requiring painting or spraying afterwards.
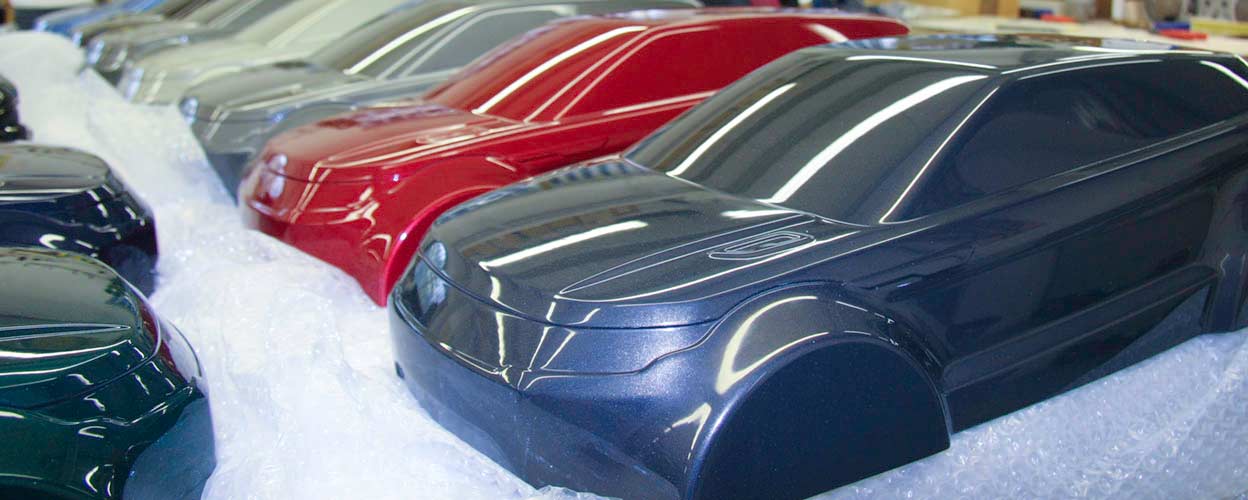
Why you might want to use low volume manufacturing
- When anticipated production quantities are low.
- To test a new product or design before committing to mass production.
- To produce items on-demand without the need to maintain large inventory levels.
- To create customized or personalized products.
- To save money on production costs for small quantities.
Low volume manufacturing strategies, which are also commonly known as rapid manufacturing or low batch manufacturing are used by businesses of all types that make plastic components with injection moulding. It may assist in reducing the moulding time to speed up the production of your goods and deliver authentic material in advance. Moulding costs are considerably lower than traditional techniques.
Advantages of using a Low Volume Manufacturing service
- Save on production costs
- Reduce moulding time
- Get actual material in advance
- Speed up the production process
High mix low volume manufacturing
High mix low volume manufacturing is a type of production process characterised by high customisation levels and low volume output.
This type of manufacturing is typically used for products that are produced in small batches or for products that require a high degree of customization. Low volume production & low volume manufacturing are terms that are often used interchangeably to refer to high mix low volume manufacturing.
Bring your visions to life today
We are at the forefront of the additive manufacturing revolution, providing businesses with the tools they need to bring their visions to life. Get an instant quote for 3D printed parts or get a bespoke quote for a larger, complex project.
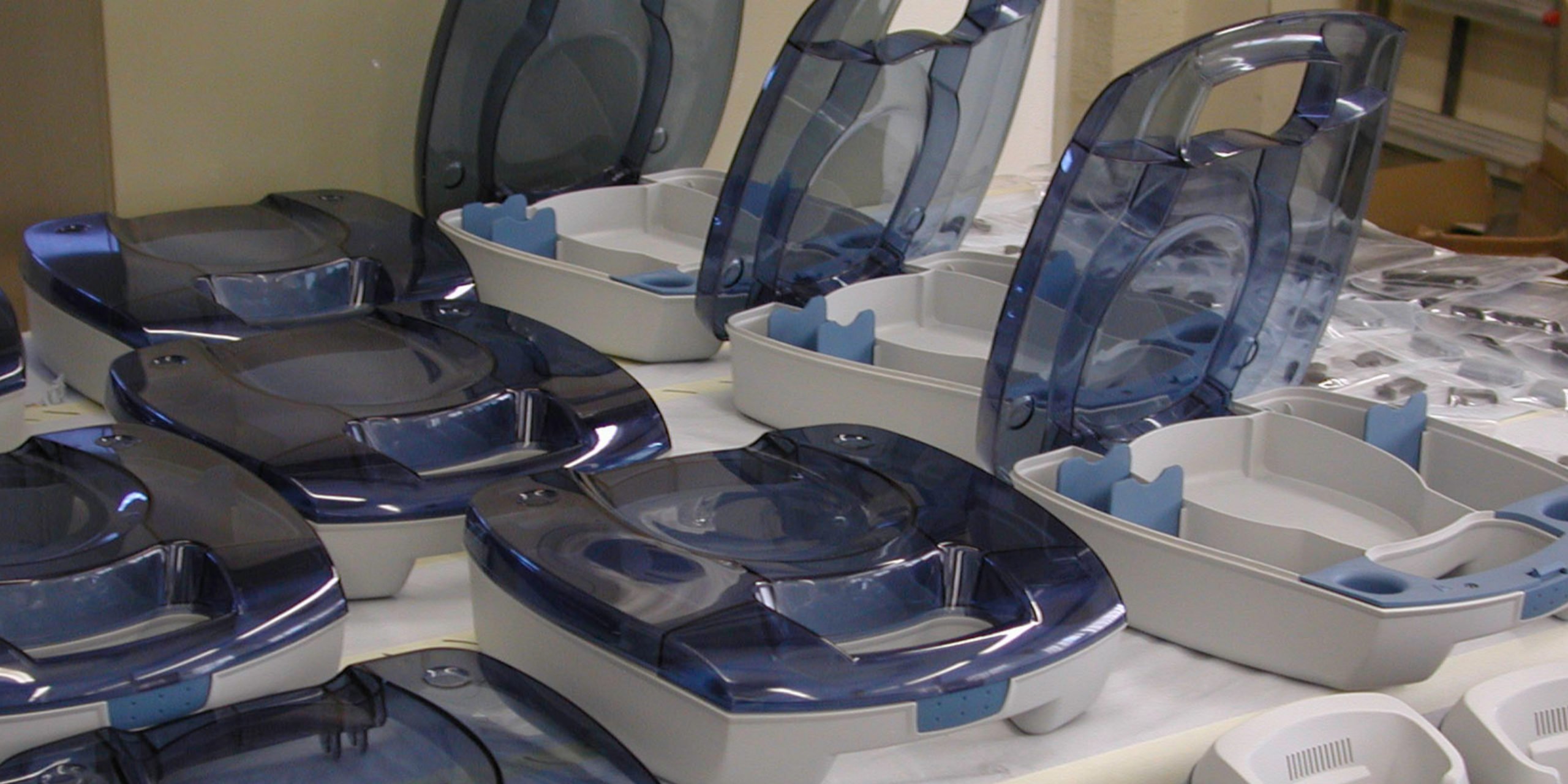