UK’s Leading Vacuum Casting Services
We can replicate components, often used in the prototype phase of product development. Strong, durable polyurethane (PU) resin components can be produced from silicone tools.
Vacuum Casting Services Redefined
At Malcolm Nicholls Ltd, we deliver premium vacuum casting services, ideal for low-volume production and prototyping. This method uses silicone tools crafted from expertly finished 3D-printed masters, ensuring precise replication of components with production-grade finishes. Our process is particularly suited for the prototype phase of product development, offering strong and durable polyurethane (PU) resin components.
With a wide selection of PU resins available, we can tailor materials to closely simulate engineering plastics or elastomers. Whether you need prototypes or high-quality vacuum casting parts, our expertise ensures exceptional results that meet your exact requirements.
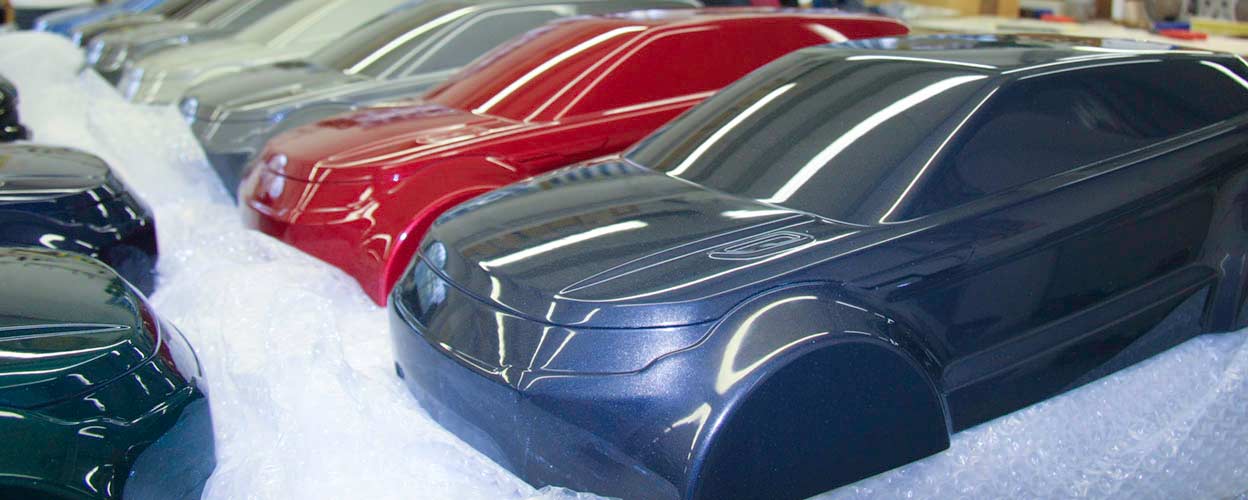
Bespoke Vacuum Casting & Rapid Prototyping Services
- “Parts can be produced in a wide array of materials to simulate most engineering plastics”
- Masters from any source or 3D printing technology are used to produce silicon tools from which castings can be produced in a wide array of materials to simulate most engineering plastics.
- We can produce Polyurethane (PU) castings in the following material simulants or properties: ABS, Polypropylene, Nylon, Glass-filled Nylon, Polycarbonate, TPE, Hytrel, HDPE, etc. Temperature-specific materials, flexible materials with A Shore ratings as low as 30A up to 90A and D Shore ratings also.
- In general MNL’s silicone tools are guaranteed to produce a minimum of 30 castings per cavity¥
- Elastomeric resins yield many more components and up to 50 castings per cavity are possible.
- Tools are available in multi-cavity versions in order to produce larger quantities quicker and more economically.
- Metal inserts are used to hold tight tolerances in bores and critical areas.
Vacuum Casting Services: Bridging the Gap between Prototyping and Low-Volume Production
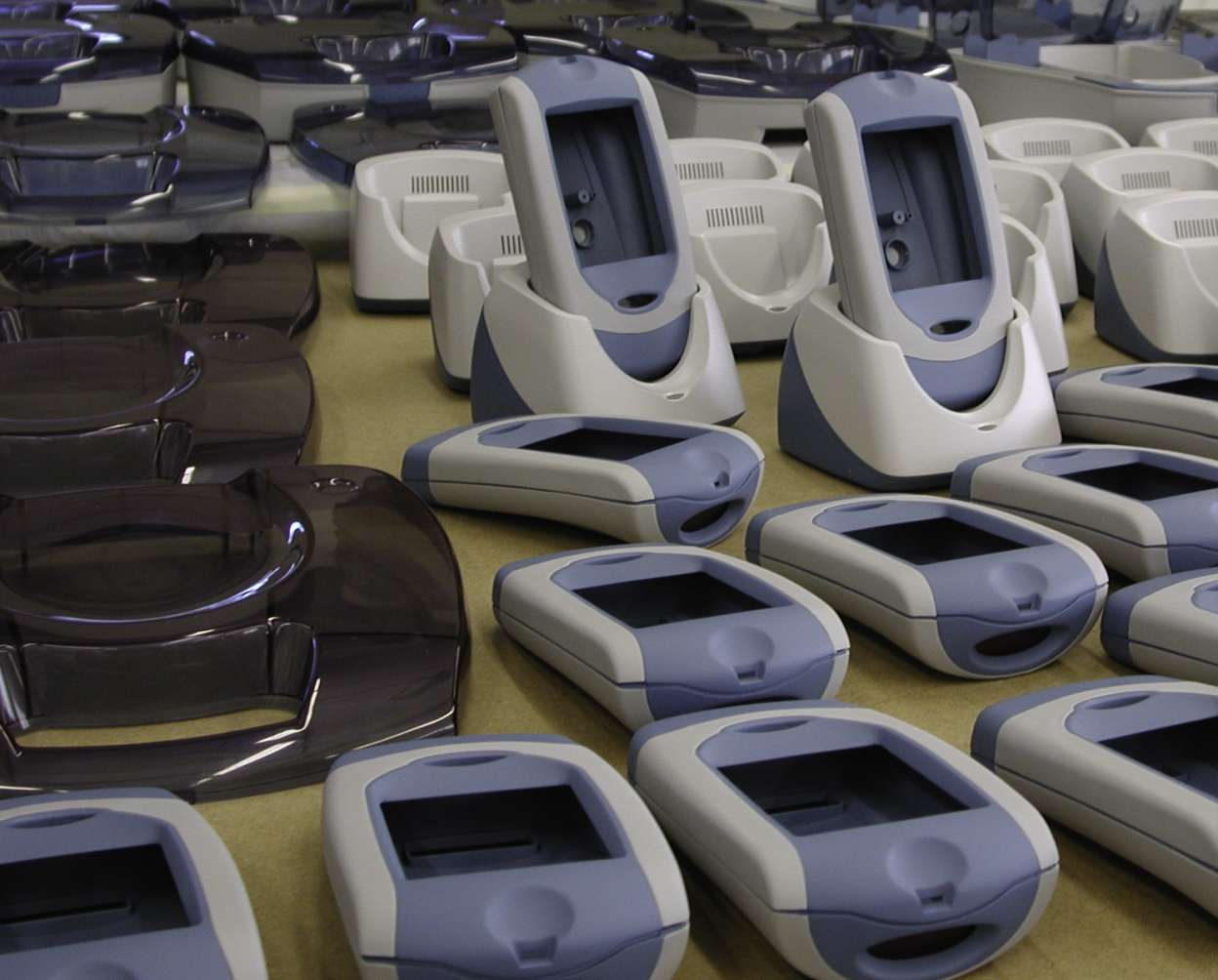
Vacuum casting fits perfectly into the low-volume production cycle due to several key advantages:
- Cost-effective tooling: Compared to injection moulding, which requires expensive metal tools, vacuum casting uses reusable silicone molds that are cheaper to produce. This makes it ideal for smaller production runs where high upfront tooling costs wouldn’t be justified.
- Faster turnaround times: The process of creating a silicone mold is quicker than traditional methods, allowing you to get parts manufactured faster. This is crucial for low-volume production where speed and agility are important.
- Flexibility: Vacuum casting can handle a wider range of part geometries compared to some other low-volume techniques. This allows you to produce complex parts with intricate details without sacrificing quality.
- High-quality parts: Despite being a rapid prototyping technique, vacuum casting delivers parts with excellent surface finish and good dimensional accuracy, making them suitable for functional applications.
Overall, vacuum casting bridges the gap between prototyping and full-scale production by offering a cost-effective and rapid way to manufacture small batches of high-quality parts.
Industry Leading Vacuum Casting & Overmoulding Solutions
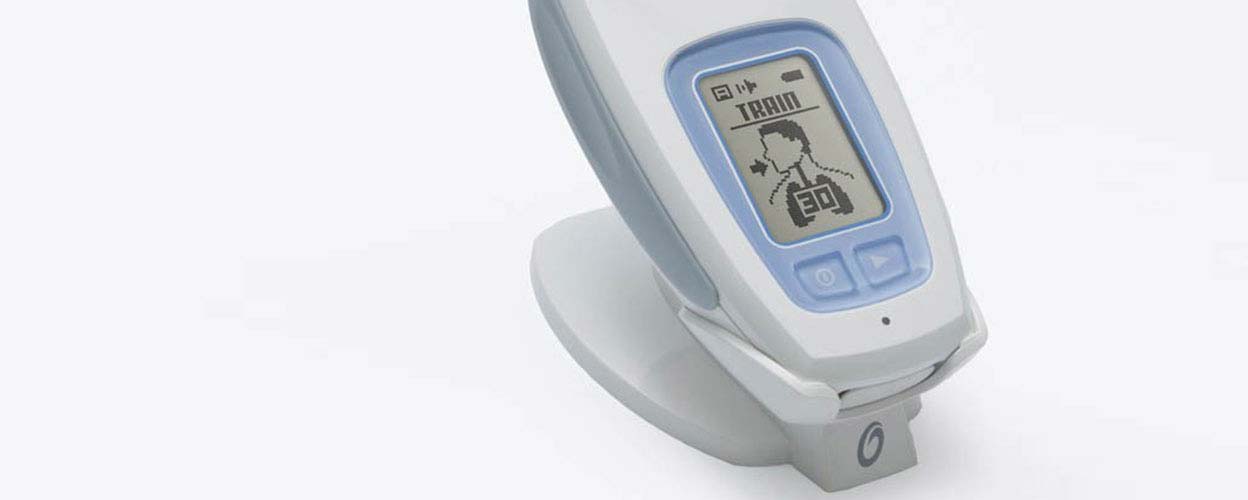
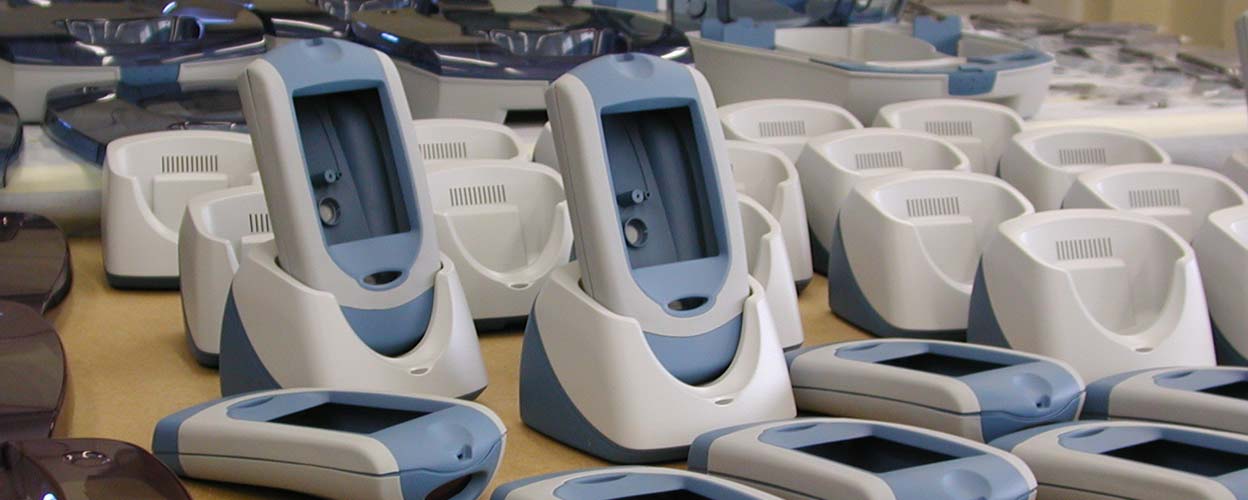
Overmoulding stands as an intricate process, wherein a secondary layer of material seamlessly integrates with an existing substrate within the realm of vacuum casting. The outcome is nothing short of remarkable — an amalgamation of materials that not only augments functionality, durability, and aesthetic appeal but also proves to be a game-changer in the new product development cycle. This technique provides unparalleled design versatility.
In the realm of prototyping, over-moulding within vacuum casting emerges as a powerful tool, enabling the creation of intricately detailed parts with varying material properties. This, in turn, facilitates the development of prototypes that serve as accurate representations of the final product. The ability to merge different materials seamlessly opens avenues for innovative design solutions, enhancing the overall product development process.
Moreover, the application shines particularly bright in low-volume manufacturing scenarios. It offers a cost-effective solution tailored for the production of small batches of high-quality components. This capability is instrumental for industries and projects where limited production runs are the norm, providing an efficient and economical approach to manufacturing.
Within our state-of-the-art facilities, we have positioned ourselves to elevate your projects with precision and efficiency. The integration of over-moulding is not merely a process; it is a commitment to delivering superior results and pushing the boundaries of design possibilities.
Looking to Produce Multiple Parts?
We can produce anything from one to thousands
The Low-Volume Vacuum Casting Process
Typical applications are endless …
- Extensive product testing is achievable on multiple sets for parallel tests.
- Quick turnaround, 20 sets available within approx 2 weeks.
- Can be cheaper than 3D printing, the break-even point is approx 4-5 sets.
- Vacuum-cast components are frequently used as market research models as they are often impossible to tell the difference between them and the production items.
- Production bridge – vacuum castings can bridge the gap whilst sales are ramping up to full production..
- Low-Volume Production – PU resin components from either low-volume vacuum casting or RIM processes offer excellent strength and durability suitable for the production of low volumes.
Examples of Projects involving Low Volume Vacuum Casting
Vacuum Casting and Prototyping Services FAQ
What is Vacuum Casting?
Vacuum casting is a manufacturing process where silicone moulds are used to create high-quality prototypes and small production runs. During this process, materials are poured into a mould under vacuum removing air bubbles and ensuring high-quality output.
What are the advantages of Vacuum Casting?
- Faster turnaround times compared to traditional methods like injection moulding.
- Lower tooling costs ideal for prototypes, low-volume production runs, or complex geometries.
- Wide range of materials available with various properties for different applications.
- Excellent dimensional accuracy and smooth surface finish.
- Suitable for small and medium-sized parts with intricate details.
What are the limitations of Vacuum Casting?
- Limited production volume compared to injection moulding.
- Certain part geometries might not be suitable due to undercuts or draft angles.
- Material properties might not be as strong as some injection moulded parts.
What materials can be Vacuum Cast?
A variety of polyurethane (PU) resins can be used, offering properties like:
- High transparency
- Flexibility
- Durability
- Heat resistance
- Paintability
How long does the Vacuum Casting process take?
The turnaround time depends on the complexity of the part and the number of parts required. Malcolm Nicholls Ltd will work with you to provide an accurate estimate.
What kind of finishes can be achieved with Vacuum Casting?
Vacuum Cast parts typically have a smooth surface finish that can be left as-is, painted, or plated.
How much does Vacuum Casting cost?
Costs depend on the part size, complexity, material selection, and quantity. Malcolm Nicholls Ltd. will provide a competitive quote based on your specific requirements.
What file formats do you accept for Vacuum Casting?
We typically work with 3D CAD files in formats like STL, STP a full list can be found on this pop up here
Is Vacuum Casting suitable for my project?
Vacuum Casting is a versatile process ideal for prototypes, low-volume production runs, and parts requiring high detail and a smooth finish. Contact Malcolm Nicholls Ltd. to discuss your project and see if it’s a good fit.
Why choose MNL for your vacuum casting and prototyping?
At Malcolm Nicholls Ltd (MNL), we bring decades of experience in vacuum casting and rapid prototyping services. Our advanced technology, skilled team, and tailored solutions ensure that every project meets the highest standards of quality and precision. We specialise in delivering exceptional results for industries ranging from automotive to consumer goods.
Get In Touch With Us For A Vacuum Casting Quote
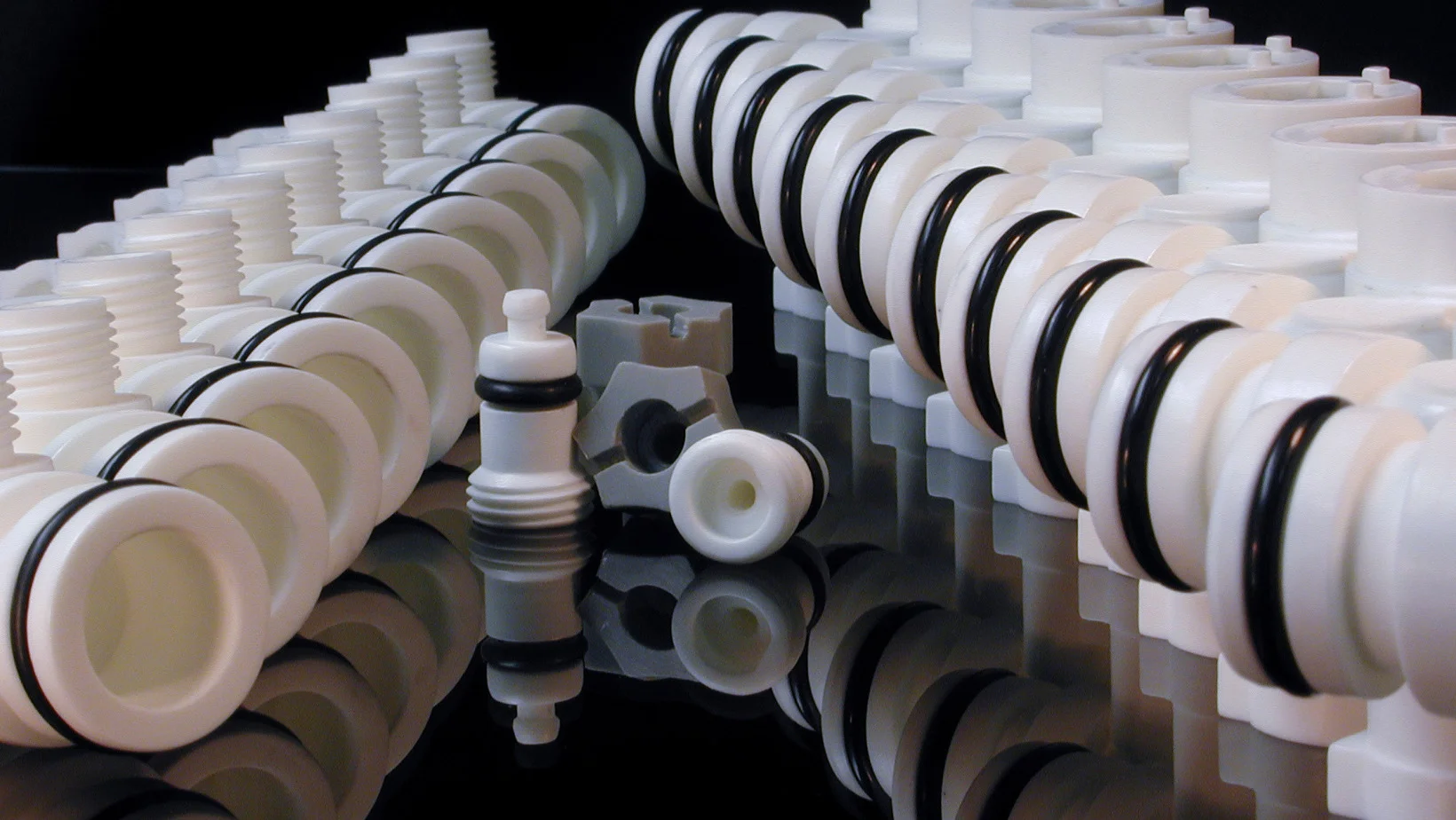
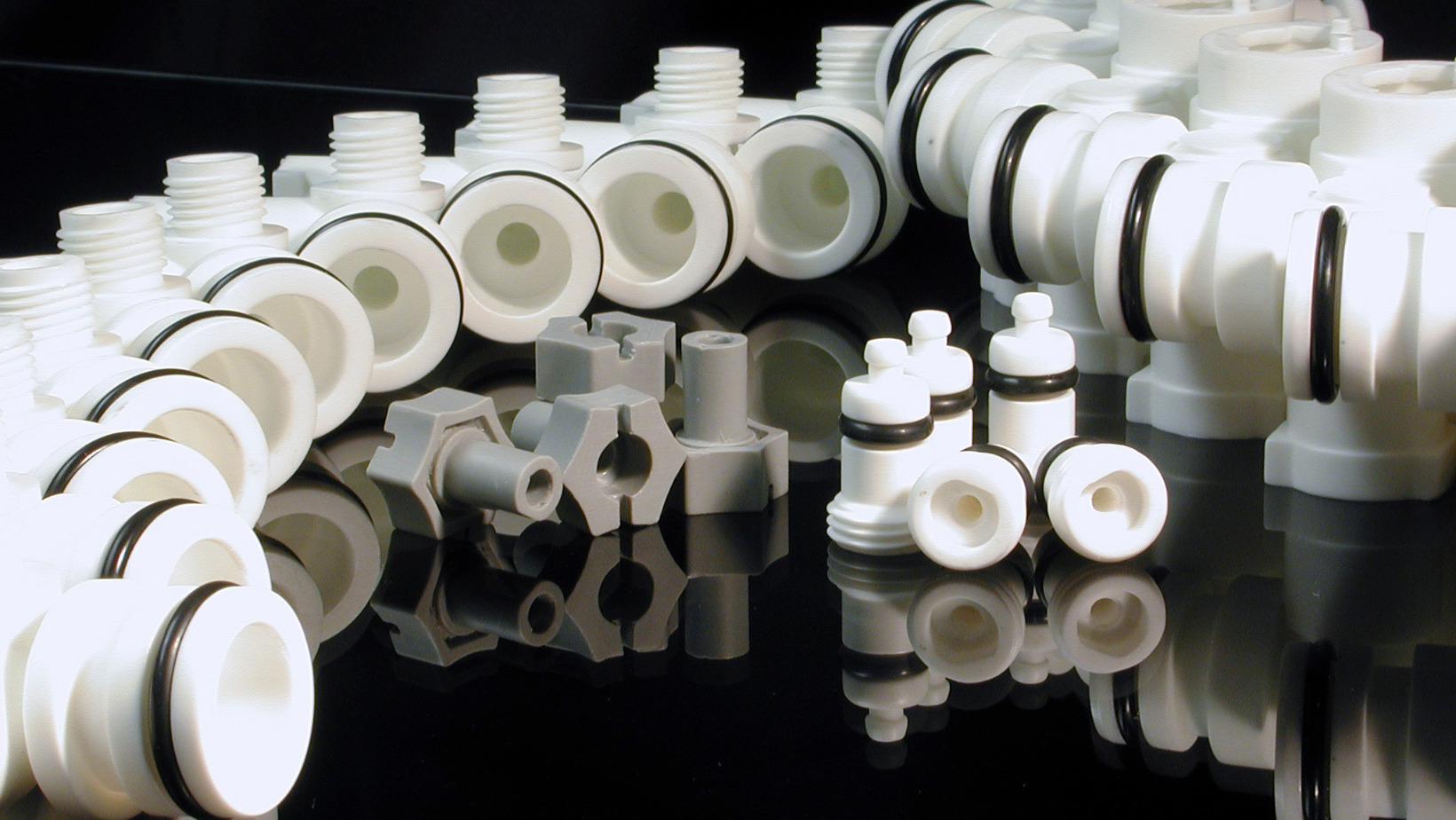