Plastic Vacuum Forming
Looking for a fast, cost-effective way to manufacture plastic parts? Malcolm Nicholls Ltd is your one-stop shop for vacuum forming in the UK. We offer a wide range of services to meet your needs, from simple prototypes to low volume production runs. Our expertise and advanced technology ensure exceptional results every time.
Two of the UK’s largest 3D printers
Custom parts delivered in days
Ideal for low volume production and rapid prototyping
Get Your Quick & Easy Project Quote Today
Benefits of Vacuum Forming
Cost Effective
Ideal for prototypes, low-volume production runs, and short lead times.
Fast turnaround
Faster production compared to injection moulding.
Versatility
Creates a wide range of shapes and sizes from various thermoplastics
Lightweight Parts
Ideal for applications requiring minimal weight.
Prototyping
Excellent for creating functional prototypes for testing and design iteration.
Made in Hours
We can help with last minute projects and offer a fast turnaround. High quality Vacuum Formed parts can be printed in a matter of days.
What is Vacuum Forming?
Get a Quote for Vacuum Forming Parts
Getting a quote for your Vac formed parts is easy! Simply upload your 3D model file and receive a quote in minutes. Want to speak to a team member? Contact usÂ
Vacuum Forming vs. Injection Moulding:
Both vacuum forming and injection moulding are effective plastic manufacturing processes, but they cater to different needs. Here’s a quick comparison:
Feature | Vacuum Forming | Injection Moulding |
Cost | Lower | Higher upfront cost |
Production Speed | Faster for low volumes | Faster for high volumes |
Complexity | Simpler shapes | More complex shapes |
Material Usage | More material waste | Less material waste |
Ideal Applications | Prototypes low-volume runs | High-volume production, complex parts |
Why Malcolm Nicholls?
UK Based
With headquarters in the Midlands, we can deliver your 3D parts nationally.
Years of Expertise
We are a family run business with decades of experience.
Finished to Perfection
A team of traditional model makers in house to give your 3D print the wow factor.
More Than Just 3D Printing
With our suite of machines and technology we also specialise in low-volume manufacturing, Vacuum Casting, CNC Machining and more.
Malcolm Nicholls Ltd: Your One-Stop Shop for Plastic Manufacturing
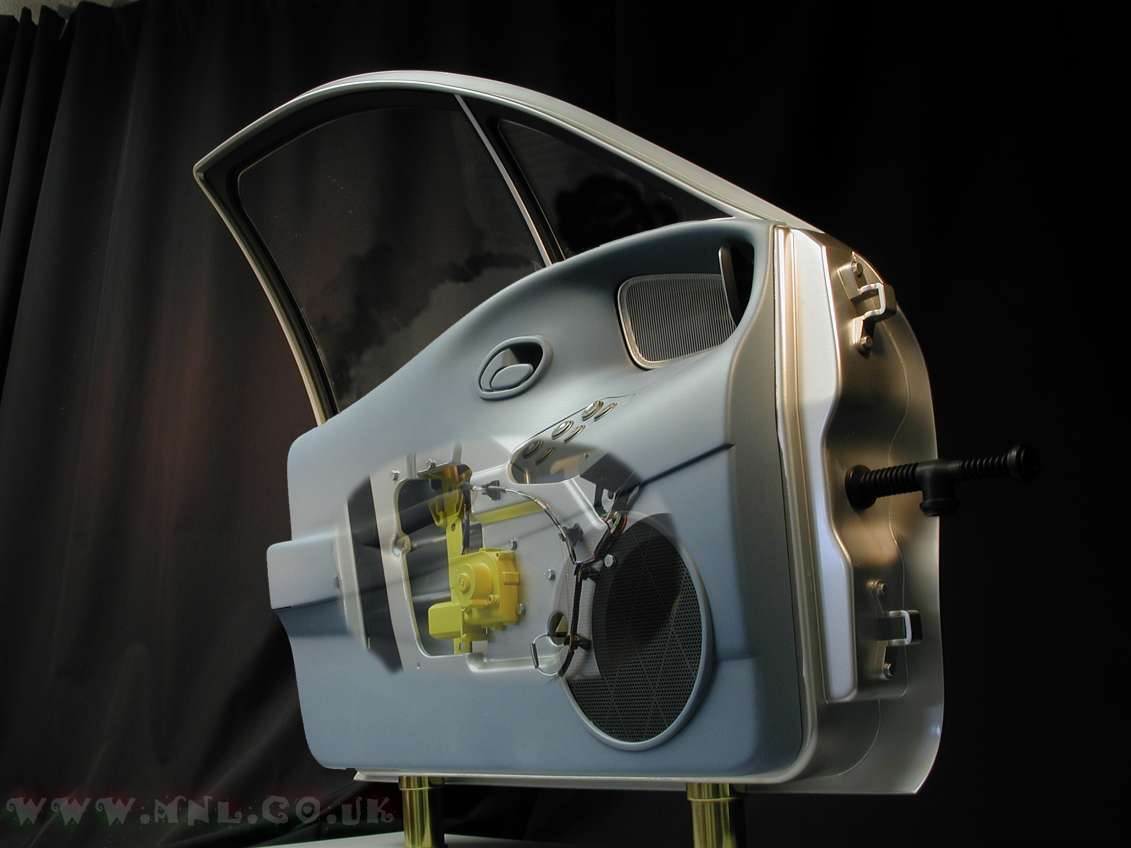
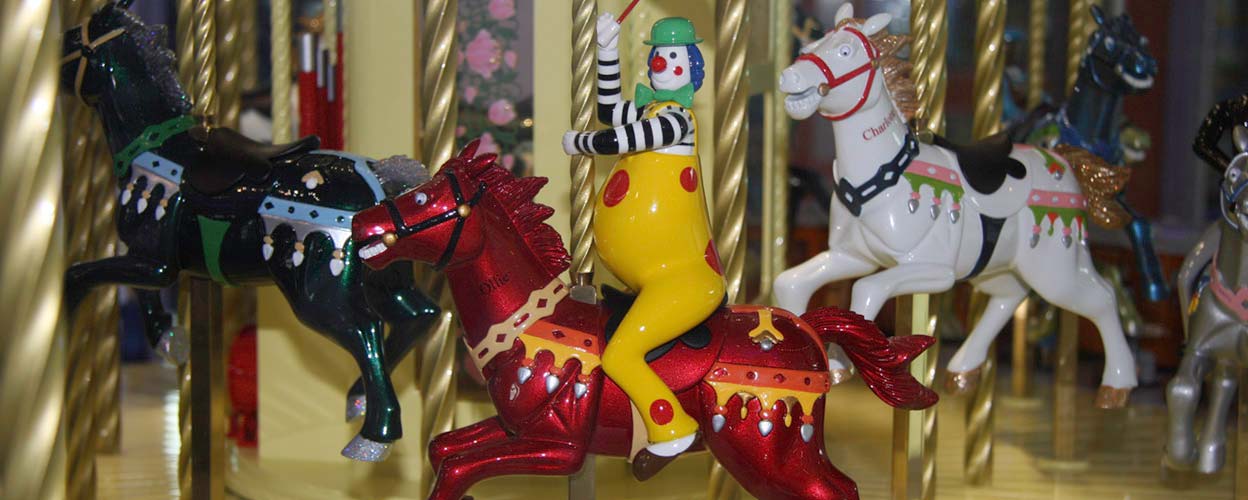
Want to know more about our Vacuum Forming Projects?
Curious to see real-world examples of our vacuum forming expertise? Dive into our previous case studies! These detailed projects showcase the versatility and effectiveness of our vacuum forming process. From prototyping innovative consumer products to crafting a large carousel for Drayton Manor Hotel, you’ll gain valuable insights into how we’ve helped businesses like yours achieve success. Let these case studies inspire your next project and see the potential vacuum forming holds for your needs!
Trusted by Industry Leaders
We have experience creating exceptional 3D printed parts for leaders across various industries. From automotive and aerospace to point of sale and packaging, we can help.
Which 3D Printing Service do I need?
Learn more about the different options we offer.
SLA
Stereolithography (SLA) also often referred to as SLA is the most widely used resin 3D printing technology. it is generally considered to provide the greatest accuracy and best surface finish of any prototyping or 3D printing process.
SLS
SLS can build functional parts, casting patterns and tooling inserts from your 3D CAD data. Our HiQ Sinterstation system (SLS 3D Printing machine) represents the future of Instant Manufacturing Technology.
FDM
Manufacturing FDM known as fused deposition modelling is the most widely available form of 3d printing. It is an additive manufacturing technology that selectively deposits molten plastic to build parts layer by layer.
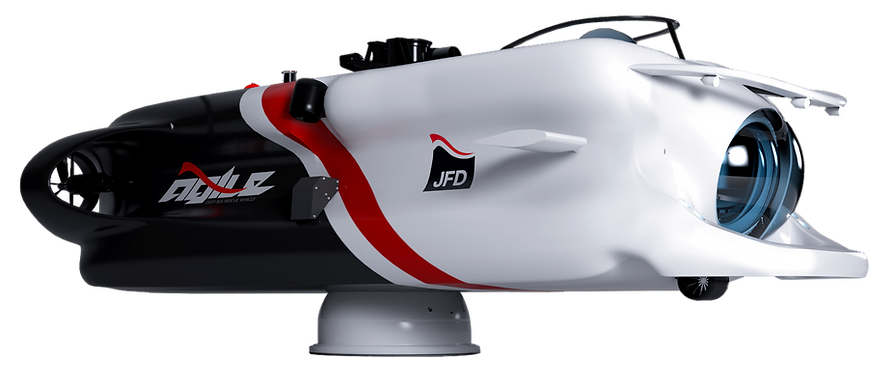
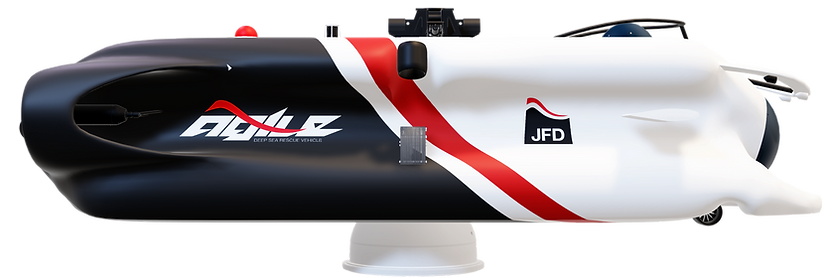
Order Your 3D Printed Parts
Getting a quote for your 3D printing project has never been easier. We offer three straightforward options to meet your needs.
Option One – Perfect for those seeking a swift and hassle-free 3D printing quote.
Option Two – If your project requires more than just printing, option two is your go-to choice, where we can provide quotes for CNC machining, surface finishing, vacuum forming, and vacuum casting for your 3D parts.
Option Three – For large, complex, intricate, or multi-part projects, look no further than option three. Give us a call, and our team will be more than happy to assist you in bringing your vision to life.
At Malcolm Nicholls Ltd, we make quoting fast, easy, and simple.
Vacuum Forming and Low Volume Manufacturing
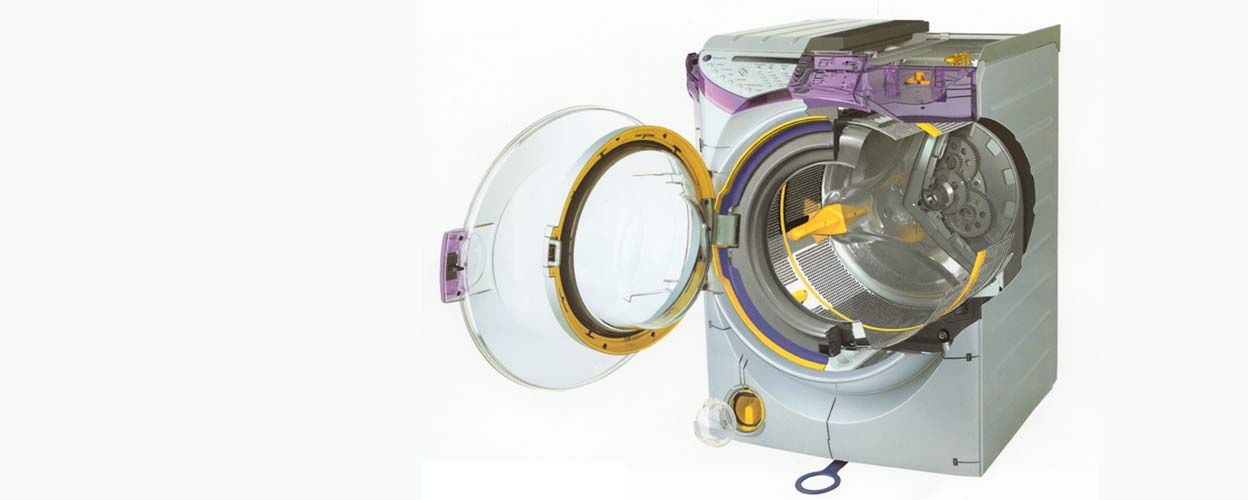
We’re often asked…
What types of plastic can be vacuum formed?
What are the typical applications for vacuum formed parts?
Can Malcolm Nicholls Ltd help with vacuum forming design?
What are the limitations of vacuum forming?
-
- Complexity:Â Vacuum forming is best suited for simpler shapes with limited undercuts or deep draws.
-
- Material Thickness:Â There’s a limit to the thickness of plastic sheets that can be effectively formed.
- Strength: Vacuum formed parts may not be as strong as injection moulded parts, especially for high-stress applications.
How does vacuum forming complement injection moulding?
Vacuum forming and injection moulding are often used together throughout the product development cycle. Here’s how:
- Prototyping:Â Vacuum forming’s fast turnaround times make it ideal for creating functional prototypes for testing and design iteration before committing to the cost of injection moulding tooling.
- Low-Volume Production:Â For low-volume production runs, vacuum forming offers a more cost-effective solution compared to injection moulding.
- Part Features:Â Certain part features, like large, flat areas, might be more efficiently produced using vacuum forming, while more complex geometries can be injection moulded.
Does Malcolm Nicholls Ltd offer finishing services for vacuum formed parts?
Yes, Malcolm Nicholls Ltd provides a variety of finishing services for vacuum formed parts to enhance their appearance and functionality. These services may include:
- Trimming and deburring
- Machining and drilling
- Painting and printing
- Assembly
Can Malcolm Nicholls Ltd help me decide between vacuum forming and injection moulding?
Absolutely! Our experienced team can evaluate your project requirements and recommend the most suitable manufacturing process based on factors like:
- Part complexity
- Production volume
- Budget
- Material selection
- Desired lead time
When can my parts be delivered?
Disadvantages of Vacuum Forming
- Limited part complexity:Â This process is not suitable for creating parts with intricate details, sharp corners, or deep draws. Depending on your project we may have a better method for your part.
- Inconsistent wall thickness and uniformity:Â Vacuum forming can result in parts with uneven wall thickness, which can affect their strength and functionality.
- High cost for large batches:Â While good for low-volume production, vacuum forming becomes less cost-effective for producing large quantities of parts.
- Additional finishing costs:Â Vacuum formed parts often require trimming, sanding, or other finishing processes, which add to the overall cost.
By considering these disadvantages, you can make informed decisions about whether vacuum forming is the right process for your project.
Get in touch
Address
Waterloo Industrial Estate, Waterloo Cres, Bidford-on-Avon, B50 4JH
Call Us
01789 490382
Email Us
quotes@mnl.co.uk