Written by Ross Nicholls
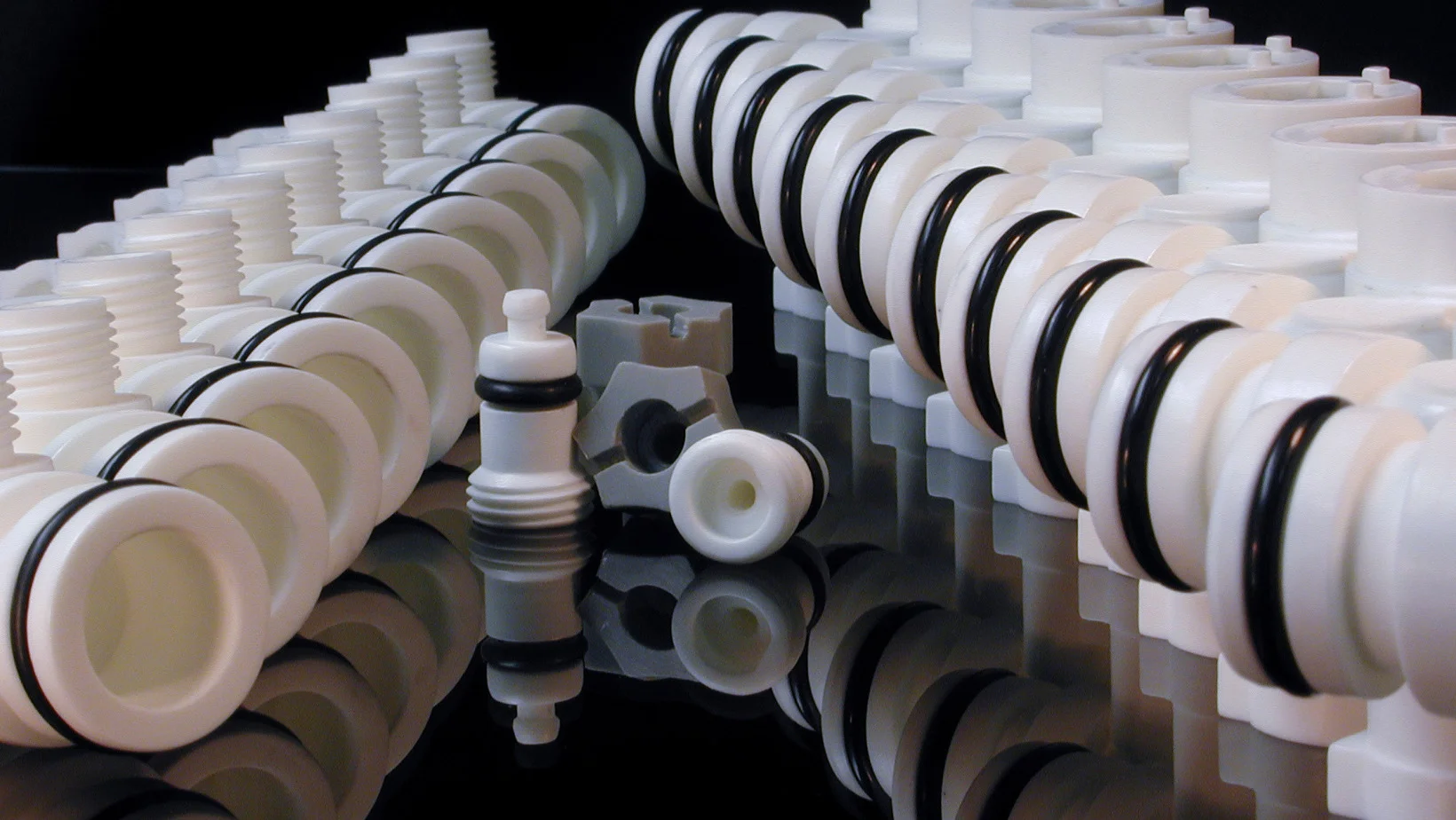
Increased demand for Direct Digital Manufacturing
Whether you call it low volume production, low volume manufacturing, low volume prototyping or even the new buzzword of Direct Digital Manufacturing (DDM) it all ultimately means the same thing. DDM for short is defined as using an additive manufacturing technology to produce end-use parts or manufacturing tools.
At MNL we are seeing an increase in the demand for low volume production services. After a recent evaluation of what we have been working on over the last 6 months, we spotted a large portion of our projects have come from direct digital manufacturing.
DDM is becoming more widely adopted because of its ability to produce manufactured parts quickly and cost-effectively this is compared to traditional manufacturing methods such as low volume injection moulding.
Direct Digital Manufacturing services
Direct digital manufacturing services are an increasingly popular option as it allows for a smaller investment in tooling and materials while providing fast access to market. Small volume production also bridges the gap between initial prototypes and mass production.
Historically, manufacturing components in low quantities has always been a costly exercise. With the advent of 3D printing and vacuum casting, many constraints previously faced can now be significantly reduced. Technologies such as SLS (Stereolithography) and FDM (Fused deposition modeling) can now be used (especially for non-seen parts), to produce components in quantities as low as 1s and 2s to thousands, but still with exceptional material properties such as flame retardancy and high-heat requirements. Traditional design constraints, usually associated with injection mould tooling for example, can now be ignored enabling designers to be more efficient and reduce part count within assemblies.
How to choose between DDM companies
There are a number of direct digital manufacturing companies available so what makes Malcolm Nicholls different? There are lots of reasons to choose us, including:
- Quick turnaround times
- 3-tier pricing strategy
- Integrated project management
- 50 years of prototyping Experience
- Two of the Largest 3D printers in the UK
What are the advantages of Low Volume Vacuum Casting, also known as “Silicon Tooling” or “PU moulding”?
- Rapid Timeframes – data to desk in rapid timeframes
- Cost Saving – Parts built directly from digital data, no need for tooling.
- Part Consolidation – Combine multiple components into one.
- Short-Run Manufacturing – DDM is an ideal solution when you need only a few thousand parts.
- Complex Parts Made Easy – Building in layers allows unlimited freedom in your design.
- Innovation – The ability to design without the constraints of traditional manufacturing techniques.
Take a look at what services we offer
Related Articles
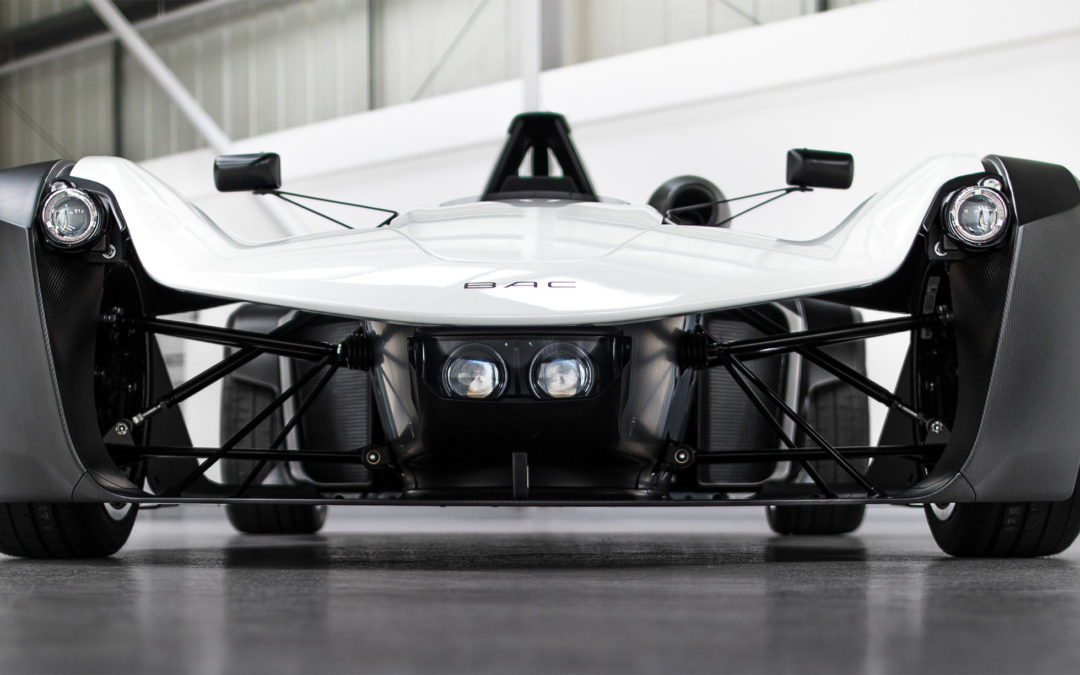
Investing in our future with large part 3D printing
Investing in our future - 3D printing large parts As Malcolm Nicholls Ltd celebrates our 50th year anniversary, it seems the perfect time to share the launch of a very exciting investment in large scale 3D printing for our rapid prototyping company. What's exciting is...
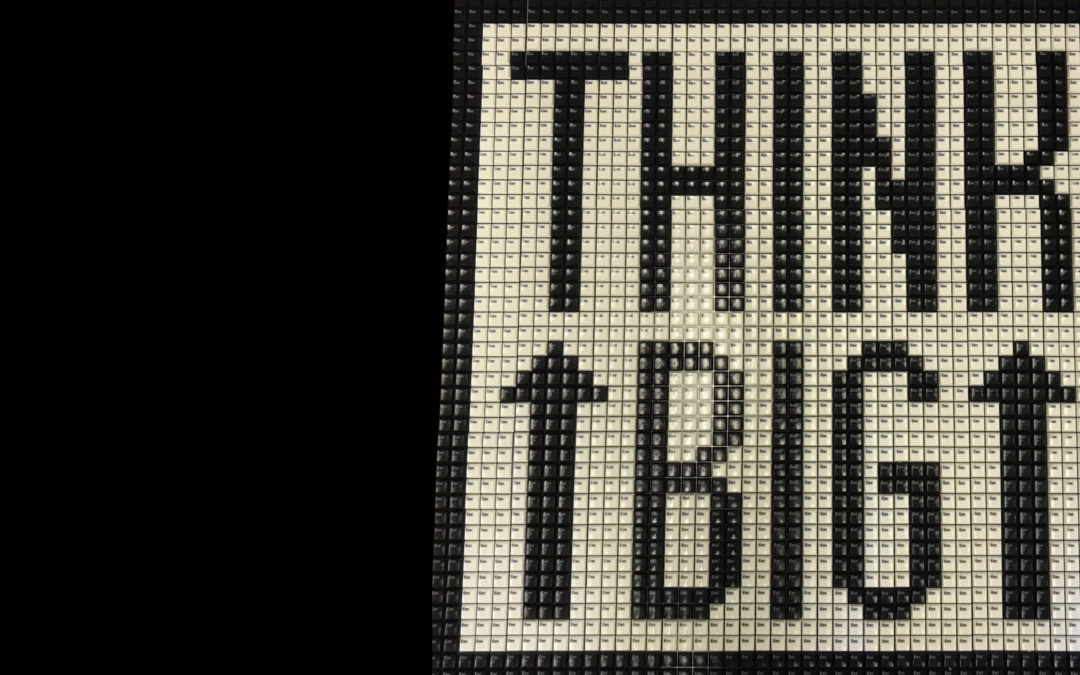
Unleash Your Creativity: A Beginner’s Guide to Custom 3D Printing
Unleash Your Creativity with a Beginners Guide To Custom 3D Printing Imagine a world where you can design and create anything you can dream of. With custom 3D printing, that world is closer than ever. But what exactly is custom 3D printing, and how does it work? This...
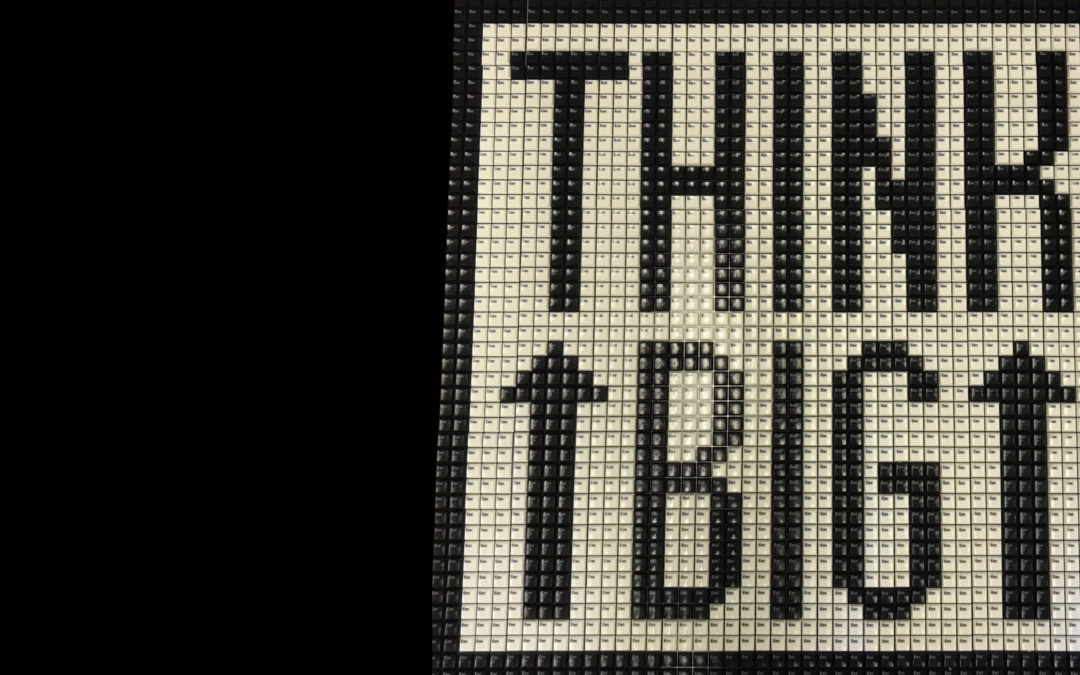
Unleash Your Creativity: A Beginner’s Guide to Custom 3D Printing
Unleash Your Creativity with a Beginners Guide To Custom 3D Printing Imagine a world where you can design and create anything you can dream of. With custom 3D printing, that world is closer than ever. But what exactly is custom 3D printing, and how does it work? This...
Stay Up to Date With The Latest News & Updates
Join Our Newsletter